MODBUS and IEC 60870-5-104 are two different communication protocols widely used in industrial automation and control systems. They have different features and are used for different purposes. There are some fundamental differences between them, which we will discuss under some main headings.
Functional Differences Between MODBUS and IEC 60870-5-104
MODBUS is a simple request-response protocol. It allows devices to read and write data to registers in other devices. The master sends a read or write request, and the slave responds to this request. The slave cannot send information or responses to the master without a request from the master. MODBUS does not provide extensive error checking or support for complex data types and is generally used for basic control and monitoring tasks. MODBUS Master/Slave support is available in all Mikrodev PLC, RTU, and SCADA products. Additionally, Mikrodev PLC and RTU products can be used in MODBUS Gateway mode. With this operating mode, which acts as a converter between MODBUS RTU and MODBUS TCP, serial MODBUS connection can be extended to the internet layers. The MODBUS Gateway mode essentially acts as a bridge, allowing Master units on the MODBUS TCP network to access Slave units on the MODBUS RTU network. Request packets coming via MODBUS TCP are converted into MODBUS RTU packets and sent to the RTU network. It also receives the response from the MODBUS RTU network and sends it to the MODBUS TCP network. On the MODBUS TCP side, the number of transactions in requests and responses must be the same, and it is the duty of the Mikrodev PLC, RTU or Gateway used as the Gateway to ensure this. Mikrodev devices that can work as a MODBUS Gateway can provide services in two directions:
1- From MODBUS TCP Master devices to MODBUS RTU Slave devices
2- From MODBUS RTU Master devices to MODBUS TCP Slave devices
IEC 60870-5-104 communication protocol has some functional features that set it apart from MODBUS communication protocol and are explained below in subheadings:
-Spontaneous Event Transfer
In the IEC 60870-5-104 communication protocol, the request-response mechanism is more advanced. The slave can transmit information to the master about itself without the need for any request from the master, and this is called “Spontaneous Event Transfer.”
In Mikrodev RTU devices used in DCS systems, various configurations related to “Send on Change and Periodic Send” features can be made from the Variable Address Table section in the Telediagram Programming Editor. Mikrodev RTU product groups offer three change methods: Level change, Percentage change, and Integral change. When a change occurs that exceeds a specified threshold, Mikrodev RTU products transmit the data to the Master, which is ViewPLUS SCADA.
-Periodic Data Transfer
The IEC 60870-5-104 protocol allows the slave to transmit data to the master at specified periodic intervals. The periodic sending frequency in Mikrodev RTU product groups can be adjusted based on the rising edge applied to the trigger input in the “IEC104 Slave Block” in your project.
-General Interrogation
In the IEC 60870-5-104 communication protocol, besides being able to respond to requests like in MODBUS, the slave can also use a more advanced query mechanism called General Interrogation. In this query structure, the master requests access to all address and values of the slave, and the slave provides all address value information to the master. Configuration in ViewPLUS SCADA can determine whether General Interrogation queries are sent to Mikrodev RTU product groups and the frequency of these queries.
Data Structures in IEC 60870-5-104 and MODBUS
MODBUS has a simple and lightweight data structure. The transmitted data includes simple data types like registers (16-bit) or coils (single bit).
IEC 60870-5-104 has a more complex and customizable data structure, and various data types can be categorized as follows:
-Digital signals
-Analogue signals
-Counters
-Commands and settings
In addition, some features that distinguish the data structure of IEC 60870-5-104 communication protocol from MODBUS communication protocol are explained in subheadings below:
-Quality Bit:
All data objects in the IEC 60870-5-104 protocol include a quality bit that indicates whether the value is valid or invalid, depending on the data type. Mikrodev RTU product groups support Quality Descriptor (QDS) bits and Quality Register Block Settings. The table below lists the Quality Bit types supported in Mikrodev RTU product groups. The usage of the Quality Bit can be configured from the variable address table section.
-Timestamp:
One of the most significant features that distinguish the IEC 60870-5-104 communication protocol from the MODBUS communication protocol is that the IEC 60870-5-104 data structure includes a Timestamp. Having a timestamp in data has the advantage that, for example, if you have a table and you are adding records corresponding to events that occur during the day to this table, when the connection between the master and slave is lost, the timestamp allows filling the table retroactively, processing data from past time periods, or overwriting it. In other words, the IEC60870-5-104 communication protocol supports historical event recording thanks to the timestamp in its data structure. ***In other words, as a result, the IEC 60870-5-104 communication protocol supports historical event recording thanks to the data structure containing a timestamp. ViewPLUS SCADA, thanks to the timestamp structure contained in the data structure of the IEC60870-5-104 communication protocol, in case of a connection lost between ViewPLUS SCADA and Microdev RTU’s for any reason, the event record that occurs can be filled into the Database for the past, it can process and overwrite data from past time periods.*** Thanks to this feature, ViewPLUS SCADA can create more meaningful and consistent reports. The ability to create a historical event record using the timestamp of ViewPLUS SCADA is referred to as “Backfilling.”
Purposes and Application Areas of IEC 60870-5-104 and MODBUS Communication Protocols
MODBUS is commonly used in small to medium-scale automation systems such as factories, warehouses, and buildings. MODBUS is a simple and cost-effective communication protocol that uses serial communication or TCP/IP. It is often used for reading and writing data from devices in industrial automation applications.
IEC 60870-5-104 is ideal for the control and monitoring of large-scale infrastructure such as energy transmission and distribution systems, water treatment plants, and traffic control centers. It is a more complex protocol used in energy automation and telemetry systems. It is designed for the remote monitoring and control of large-scale infrastructure, such as electrical grids and energy facilities.
Security and Reliability
MODBUS includes basic security measures but does not provide extensive security features. Due to data security and authentication shortcomings, it can be vulnerable to cyberattacks. Ensuring data integrity and interpreting data are challenges in MODBUS communication protocol, which relies solely on the request-response mechanism.
IEC 60870-5-104 offers more security and reliability features. It includes additional mechanisms to ensure data integrity and security. With the “Backfilling” feature in Mikrodev RTU and SCADA products, data and changes that occur when there is no connection are stored in the memory of Mikrodev RTUs operating as IEC 60870-5-104 Slaves. When the connection is restored, the data is transmitted to ViewPLUS SCADA, which acts as the IEC 60870-5-104 Master. ViewPLUS SCADA can fill historical event records logically, process data from past time periods, and overwrite data. This ensures data integrity and allows for more meaningful reporting.
In conclusion, MODBUS and IEC 60870-5-104 are two different communication protocols that meet the requirements of different industrial applications. MODBUS is suitable for simpler, cost-effective applications with lower security requirements, and it is supported in all Mikrodev products.IEC 60870-5-104 was developed for complex and safety-oriented large-scale applications. The choice of IEC 60870-5-104 communication protocol supported in the Mikrodev DCS (Distributed Control System) product line should be made depending on your specific application requirements and security needs.
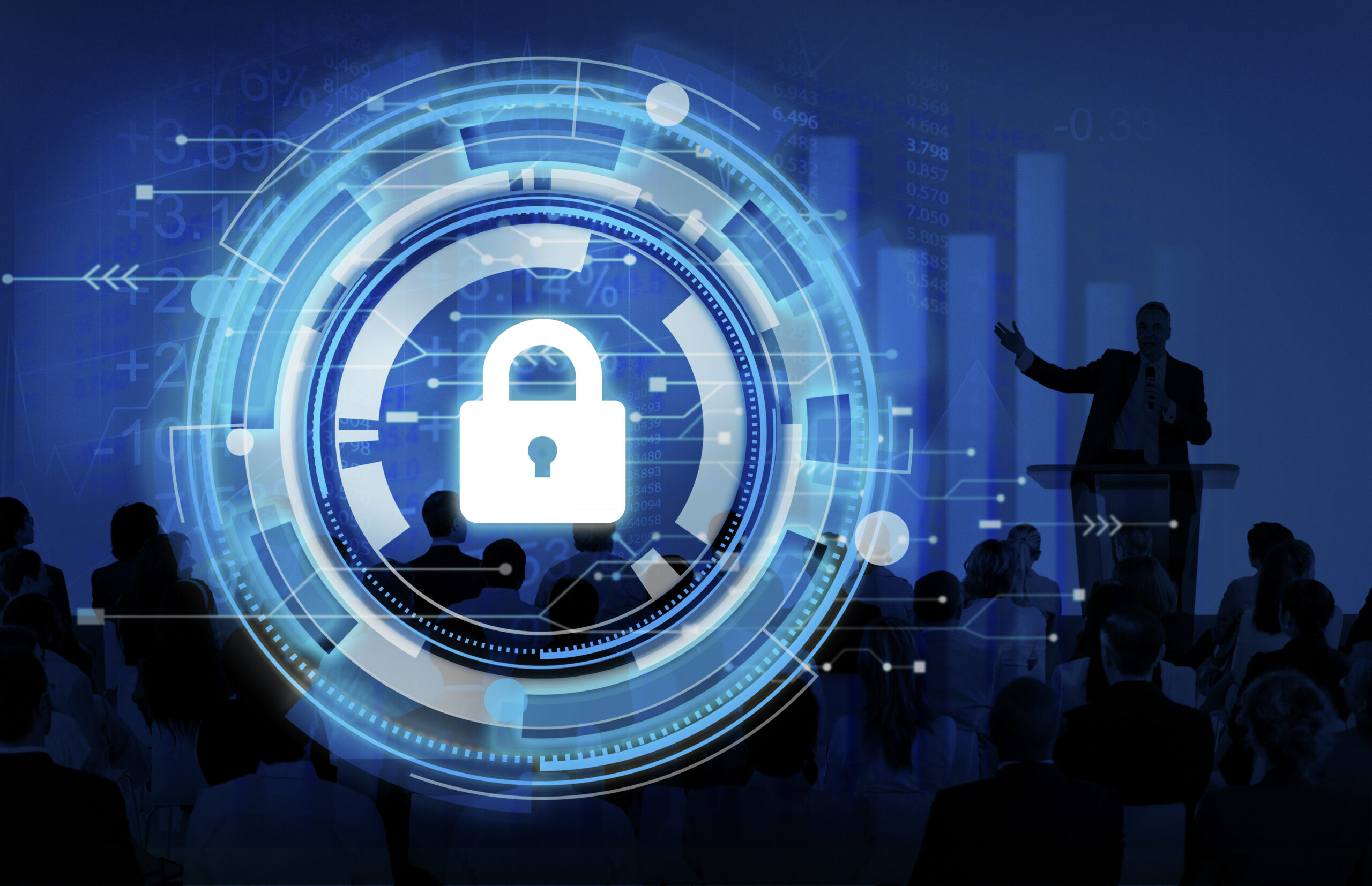
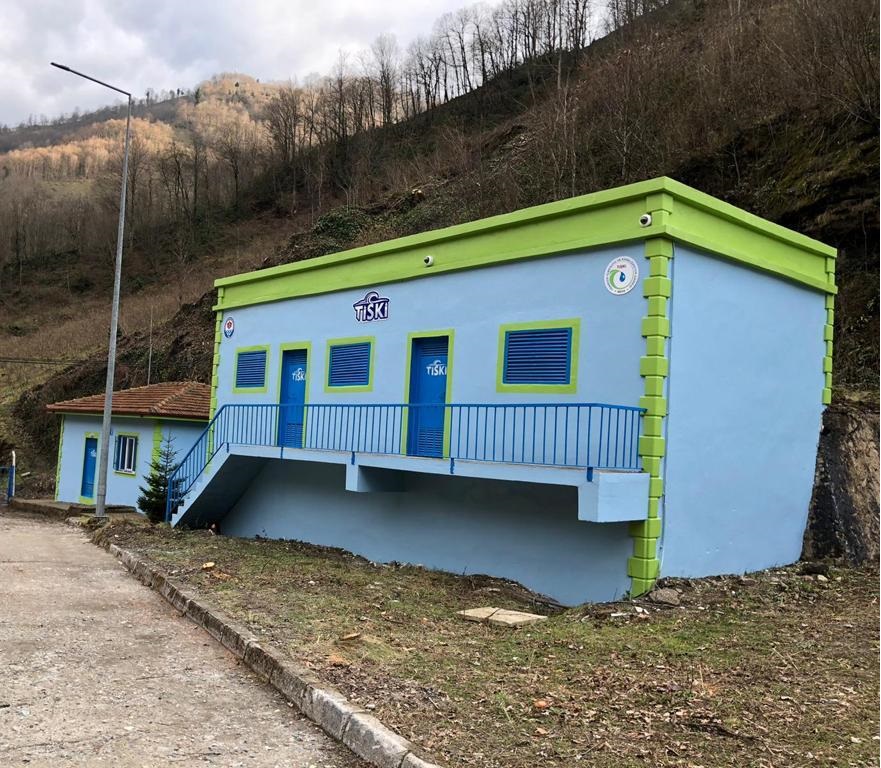
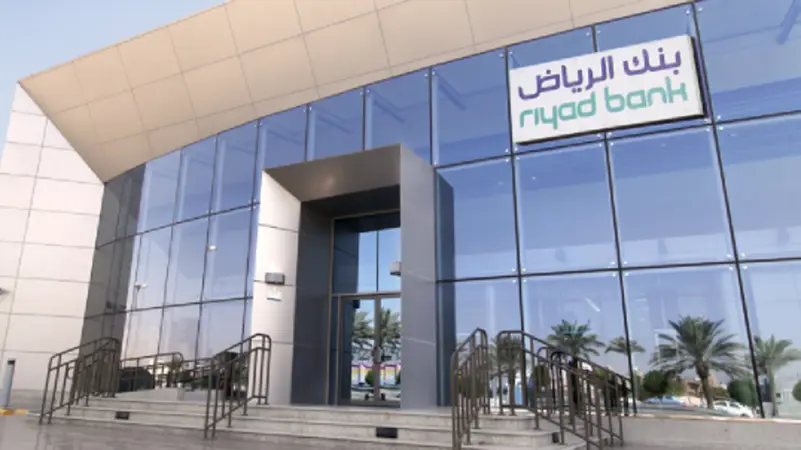
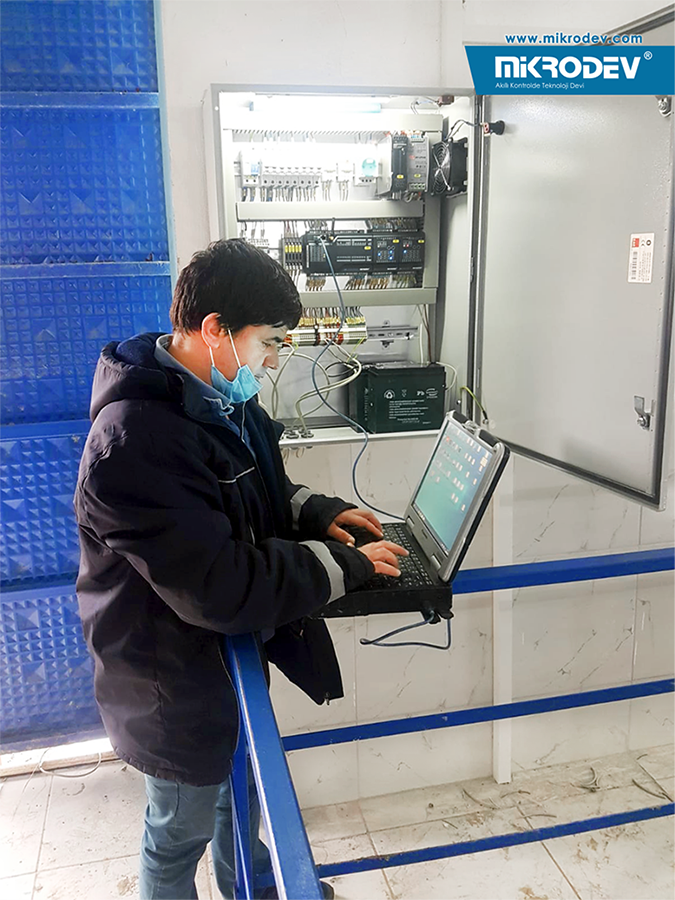
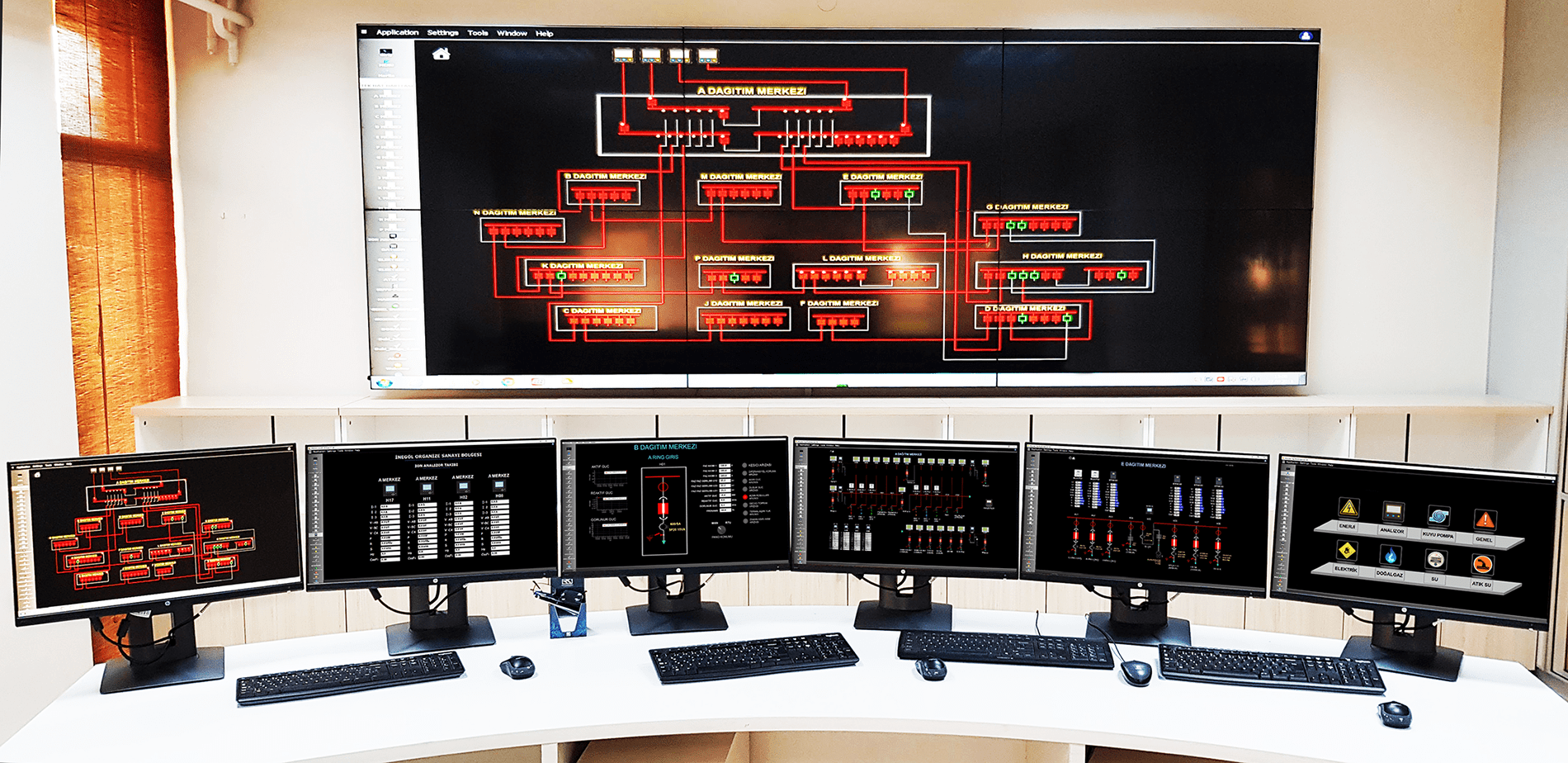
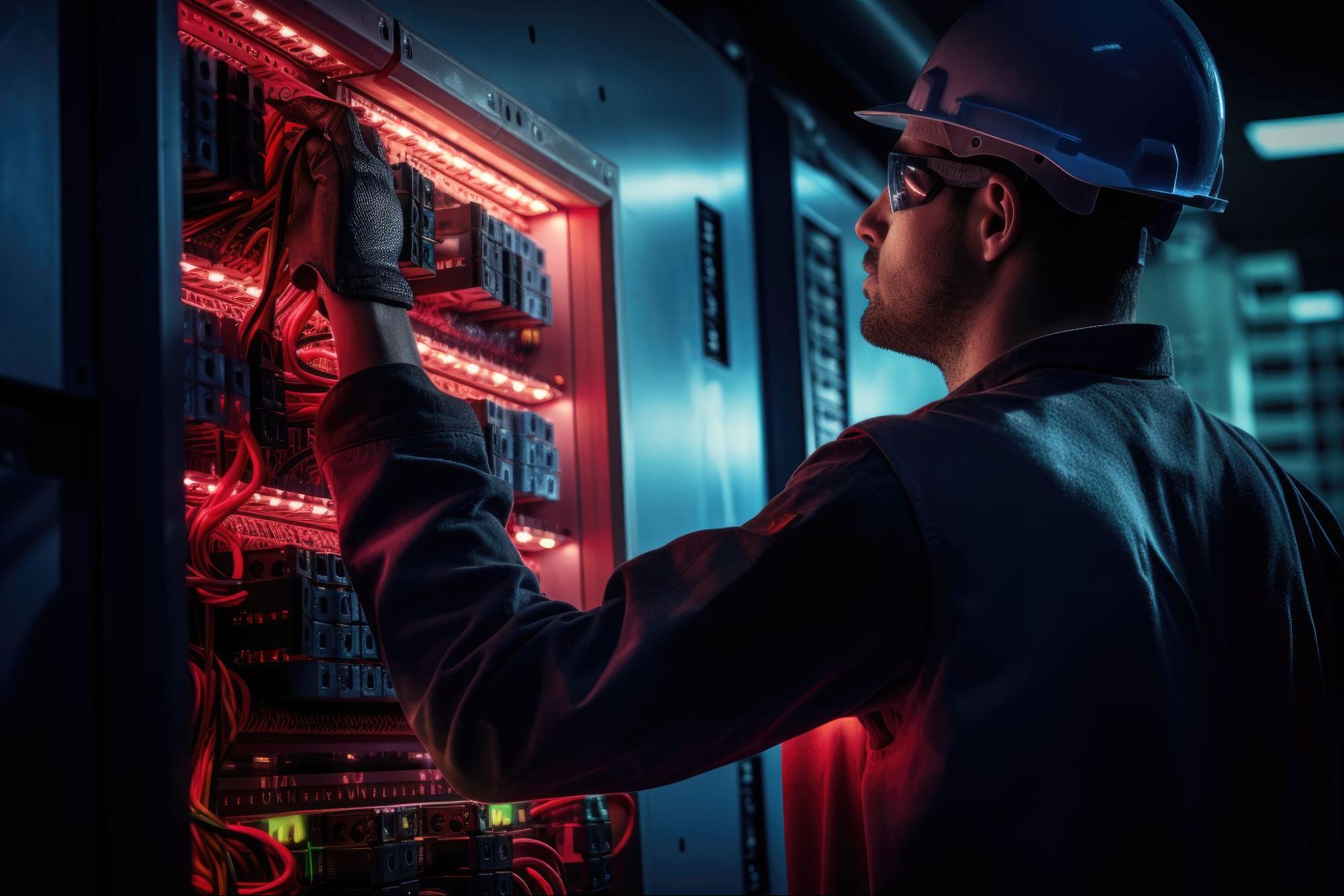
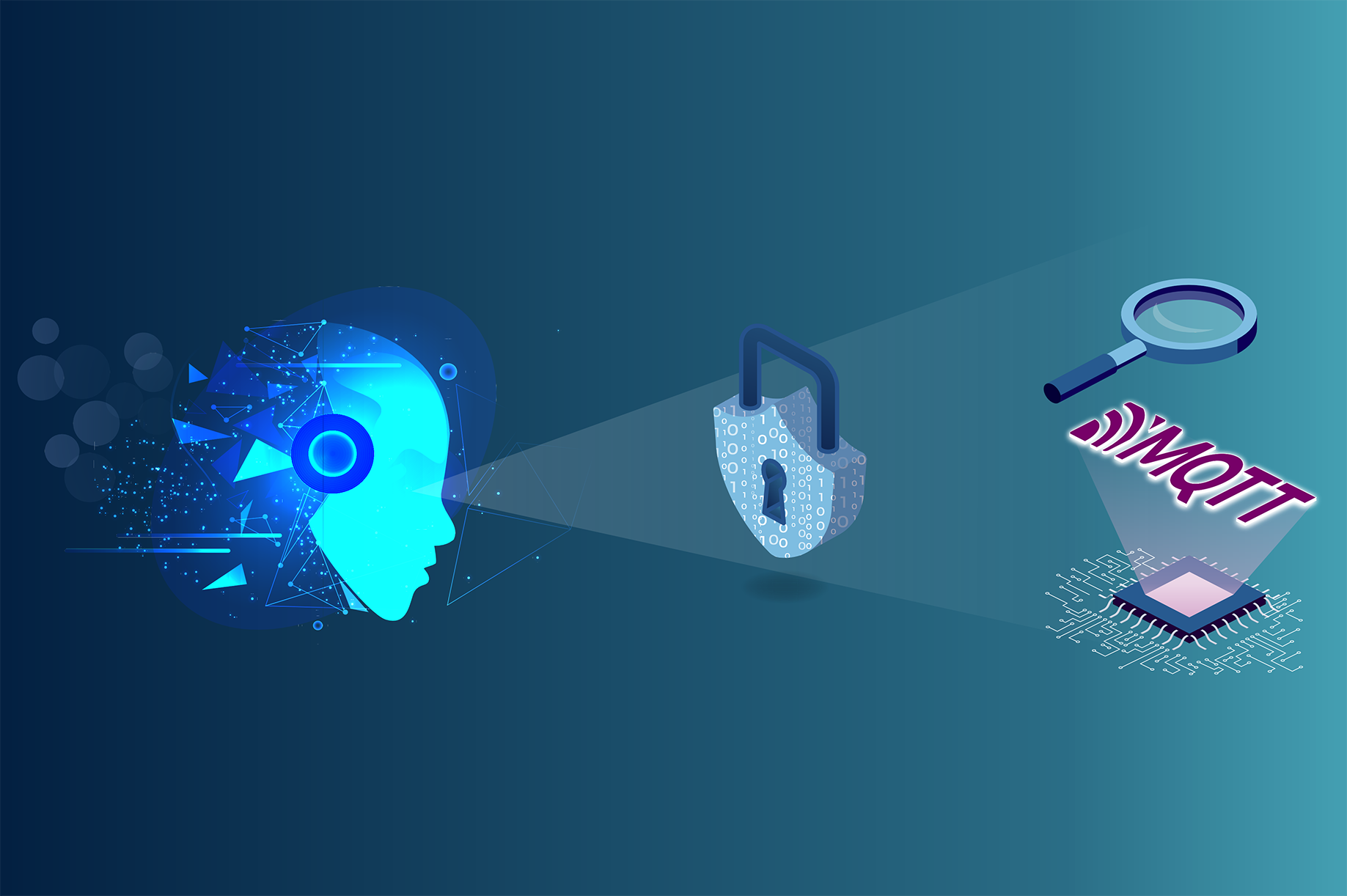
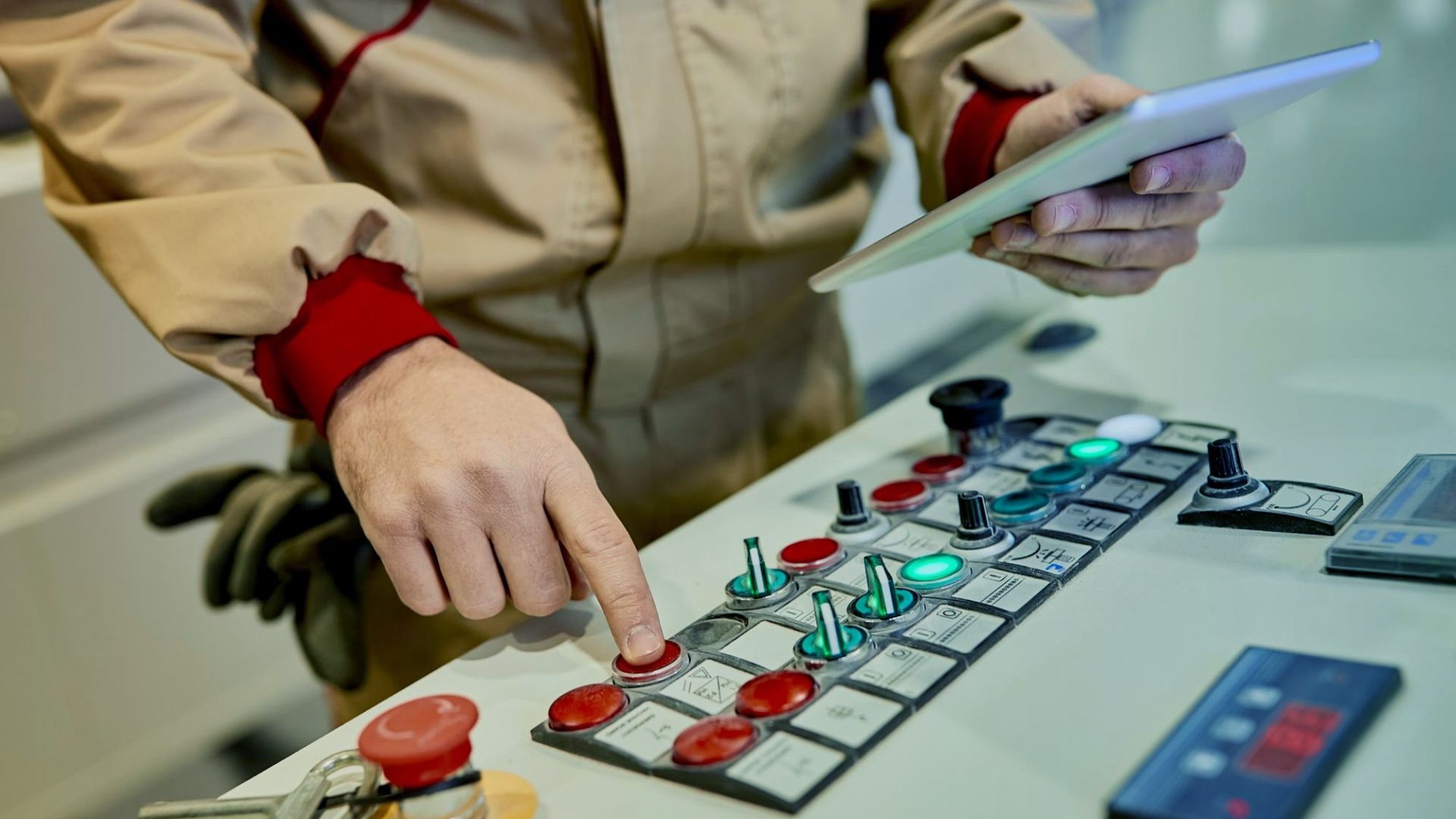
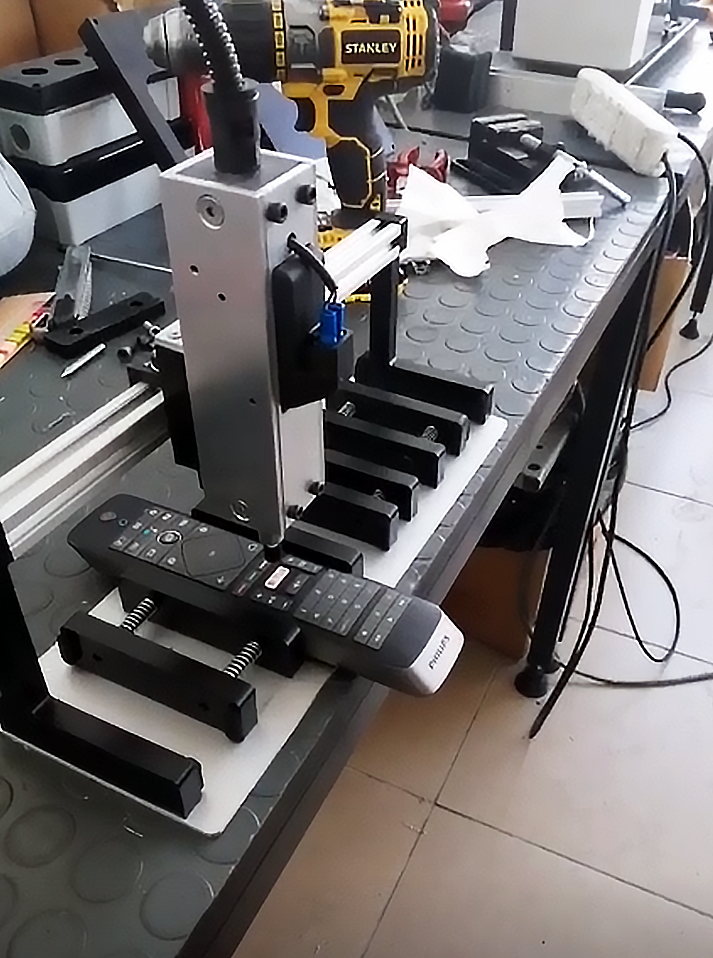
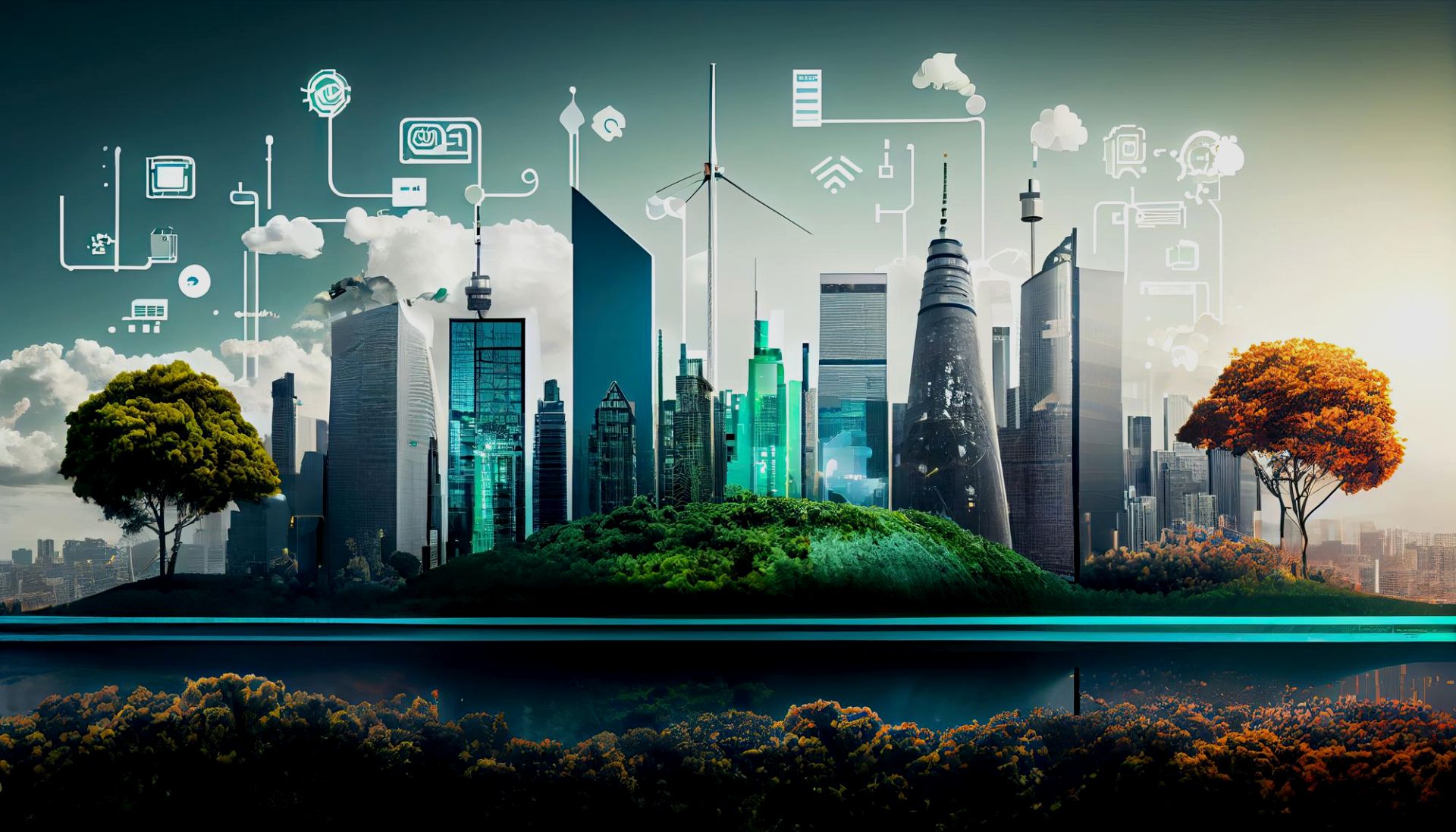