Programmable logic control systems (PLC) have become an indispensable tool of modern industrial automation. Programmable logic controllers are an essential cog in industrial systems and provide flexible, robust, and highly customizable solutions for various applications. This blog post will address the most frequently asked questions about PLCs, covering their functions, PLC controllers and communication protocols, PLC programming methods, and more. We will also highlight the advantages of using PLCs and why they have become essential to industrial automation and automation technology. Moreover, we will introduce you to the innovative PLC systems and solutions of Mikrodev, one of Turkey’s leading PLC companies for industrial automation systems and reshaping industry standards.
Stay tuned for details!
What is a PLC Meaning? What are Its Types?
A PLC is a microprocessor-based device and is an alternative to control elements such as auxiliary relays, time relays, and counters in automation loops. The software performs timing, counting, sequencing, and combinational and sequential logic operations in these devices. There are many different types of PLC controllers in automation systems; however, according to hardware setup and output modules most commonly used PLC types can be categorized as Fixed PLC (or compact PLC) and Modular PLC.
How does a PLC work?
The way a PLC works is based on a continuous scanning of a defined program. This scanning process is completed in three main steps. The PLC repeats this cycle continuously until it enters stop mode.
It’s worth mentioning that the scan cycle of a PLC can vary depending on the complexity of the program and the speed of the controller, ensuring real-time control and monitoring of industrial processes.
What is a PLC communication module?
PLC communication modules are interfaces that enable PLCs to communicate with different devices. With these modules, PLCs can exchange data with other devices. Modbus is a serial communication protocol developed in 1979 for PLCs.
Furthermore, PLC communication modules come in various types, such as RS-232, RS-485, and Ethernet modules, each designed for specific communication needs and distances.
What are PLC Communication Protocols?
Communication protocols between PLCs are server-client-based protocols that can provide communication between different devices. Modbus, the most widely used protocol in the industry, is used as a serial communication protocol thanks to its simple and robust structure. Modbus is also known as one of the oldest serial communication protocols that meet communication needs in the industrial field.
Additionally, it’s important to note that some other commonly used communication protocols in industrial automation include Ethernet/IP, Profinet, and DeviceNet. These protocols cater to different communication requirements and network configurations.
What are the Programming Languages for PLC?
PLCs are usually programmed with a program coded in a computer and then downloaded to the controller. Most PLC programming software offers Ladder diagrams or “C” programming. Ladder Logic is a traditional programming language that mimics diagrams with logical “steps” read from left to right. The most common PLC programming languages in many sources are Ladder Logic and Structured Text. Ladder Logic is a programming language designed as a ladder, similar to the schematic representation of electronic circuits. Structured Text is a structured programming language like C language.
Moreover, some advanced PLCs support programming in Structured Text, a text-based language similar to popular programming languages like C. Such adaptability empowers developers to select the language that best fits their specific application.
Which Processes can be Handled with PLCs?
PLCs are automation systems developed to serve in industrial operations. These are automation tools and devices that provide management opportunities such as time control, counting, storage, and mathematical operation functions. Hence PLCs are preferred in various procedures such as ventilation and cooling plants, packaging systems, transportation systems, the automobile industry, oil filling and washing plants, the cement industry, air conditioning and elevator plants, electro-pneumatic and hydraulic systems, and lighting and crane plants.
In addition, PLCs are indispensable in applications where precision control, data logging, and seamless integration with other automation components are required. They are extensively used in industries like food and beverage, pharmaceuticals, and renewable energy.
Why do we use PLCs?
As we mentioned previously, PLCs are automation systems developed for use in industrial areas. Using PLCs reduces errors in production and automation processes and increases the efficiency of businesses. Because PLC controllers are also easy to program and maintain and can be handled for various applications, they stand as a vital part of industrial automation. Furthermore, PLCs contribute significantly to the implementation of Industry 4.0 principles, enabling the collection of big data for predictive maintenance and process optimization.
PLC Systems and Solutions of Mikrodev
Programmable logic controller devices in Mikrodev’s product range support Modbus RTU and Modbus TCP protocols, which are the international standards for communication in industrial automation systems, and MQTT protocol for IoT applications. Mikrodev products also include “PLC GSM” technology, which enables remote monitoring and control via the GSM (Global System for Mobile Communications) network. This technology is offered with an industrial programmable controller, a type of PLC.
Mikrodev’s PLC systems are adopted in various automation fields such as building automation, energy systems, water systems, process automation, machine automation, transportation systems, IoT and telemetry applications, lighting systems, and agricultural irrigation systems. PLC controllers and PLC systems provide savings by enabling efficient use of techniques and resources. With these features, Mikrodev products offer global solutions in the industrial automation sector and systems; therefore Mikrodev’s products are utilized in diverse application fields. Mikrodev, as a leading PLC company among the
the industrial automation companies in Turkey with their product range, maintain R&D investments for automation systems and technologies.
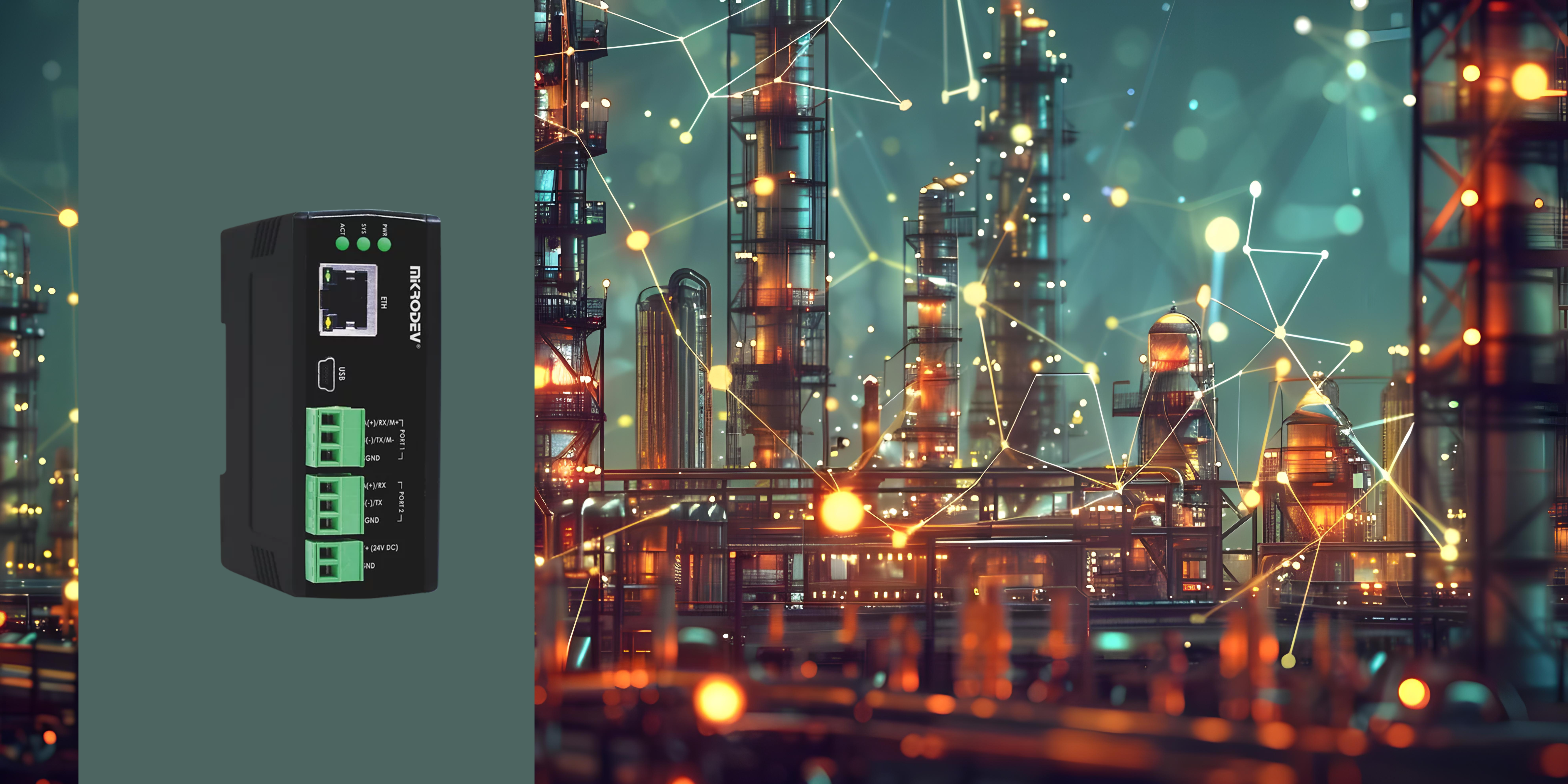
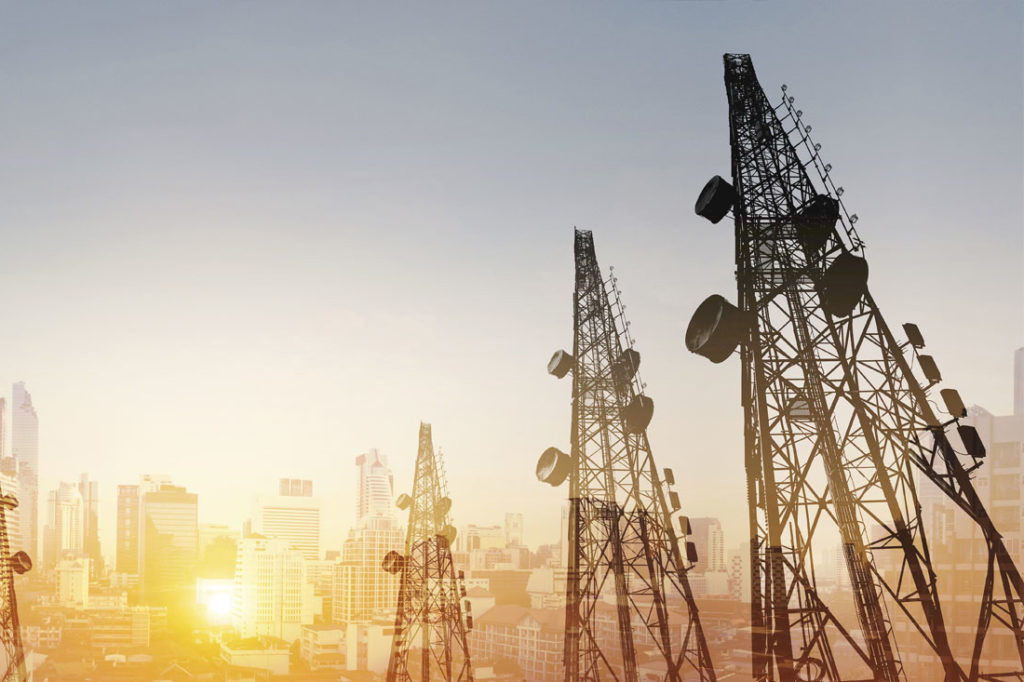
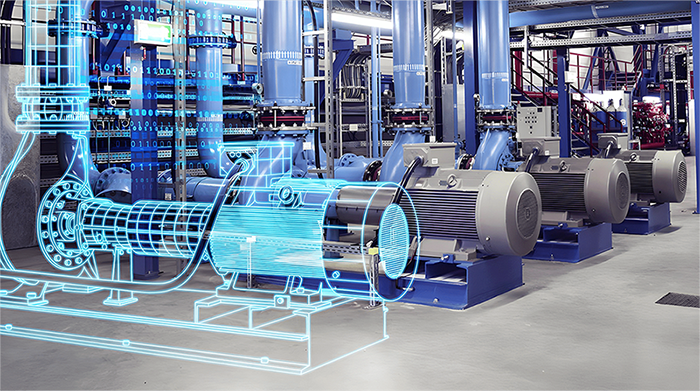
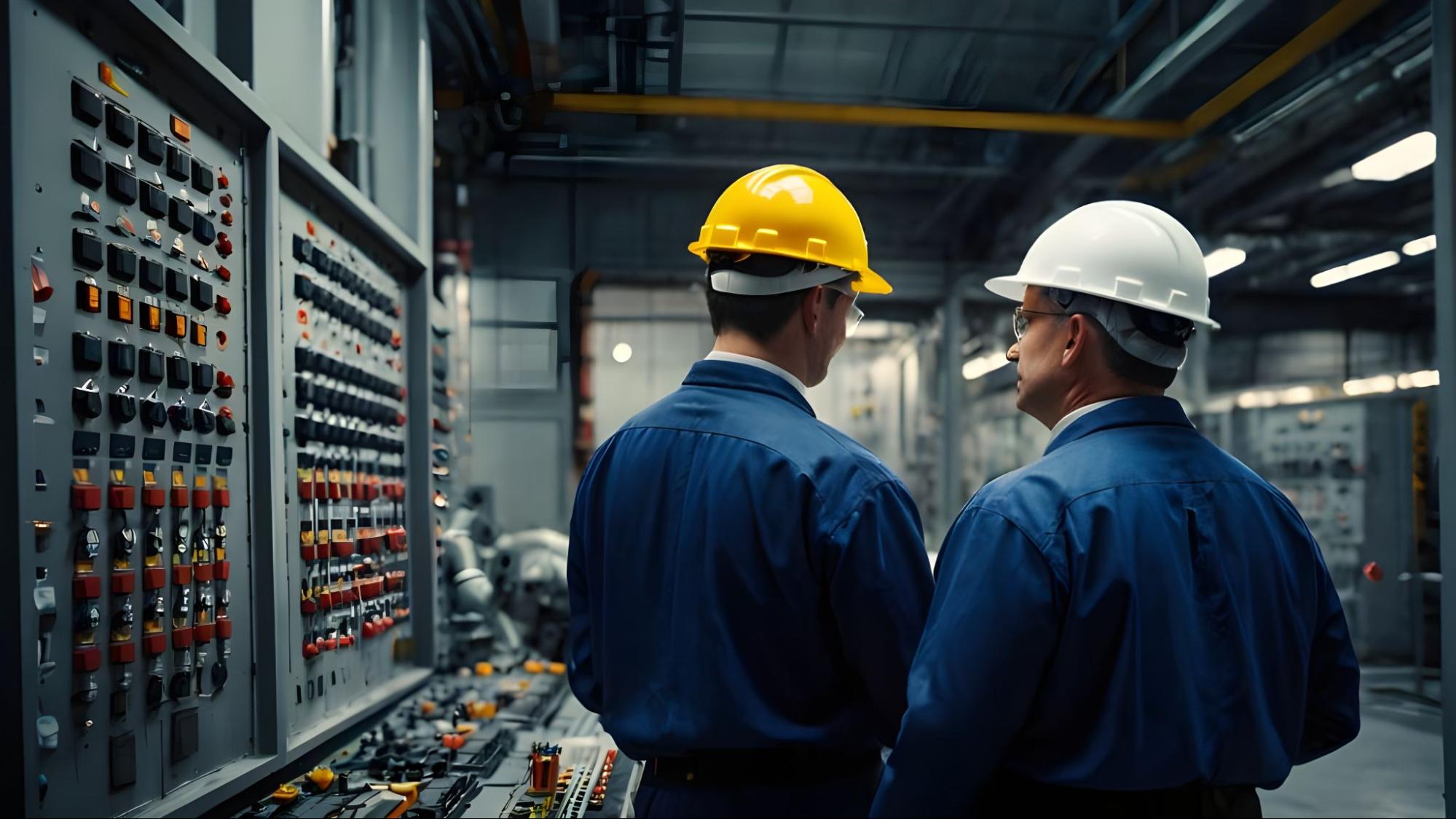
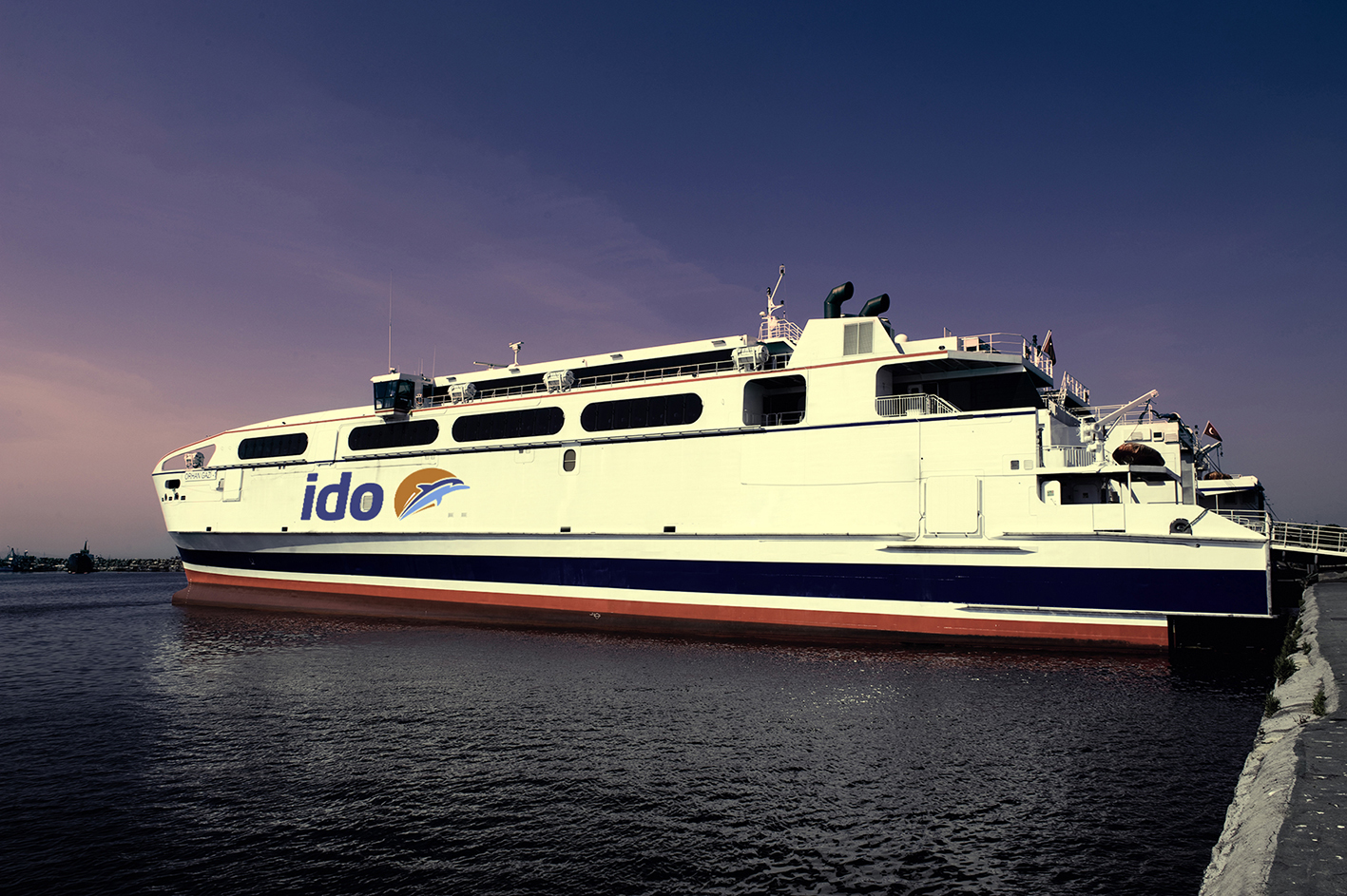
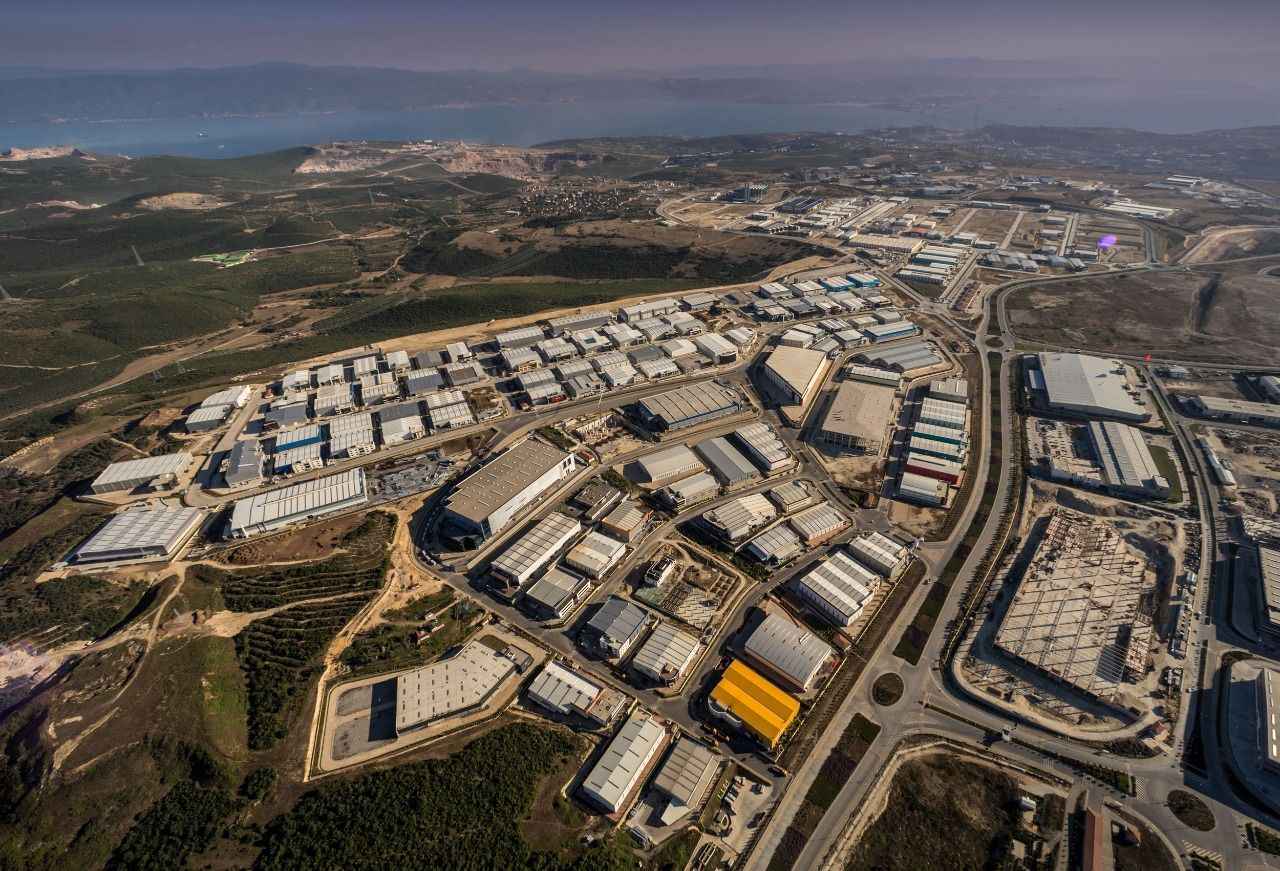
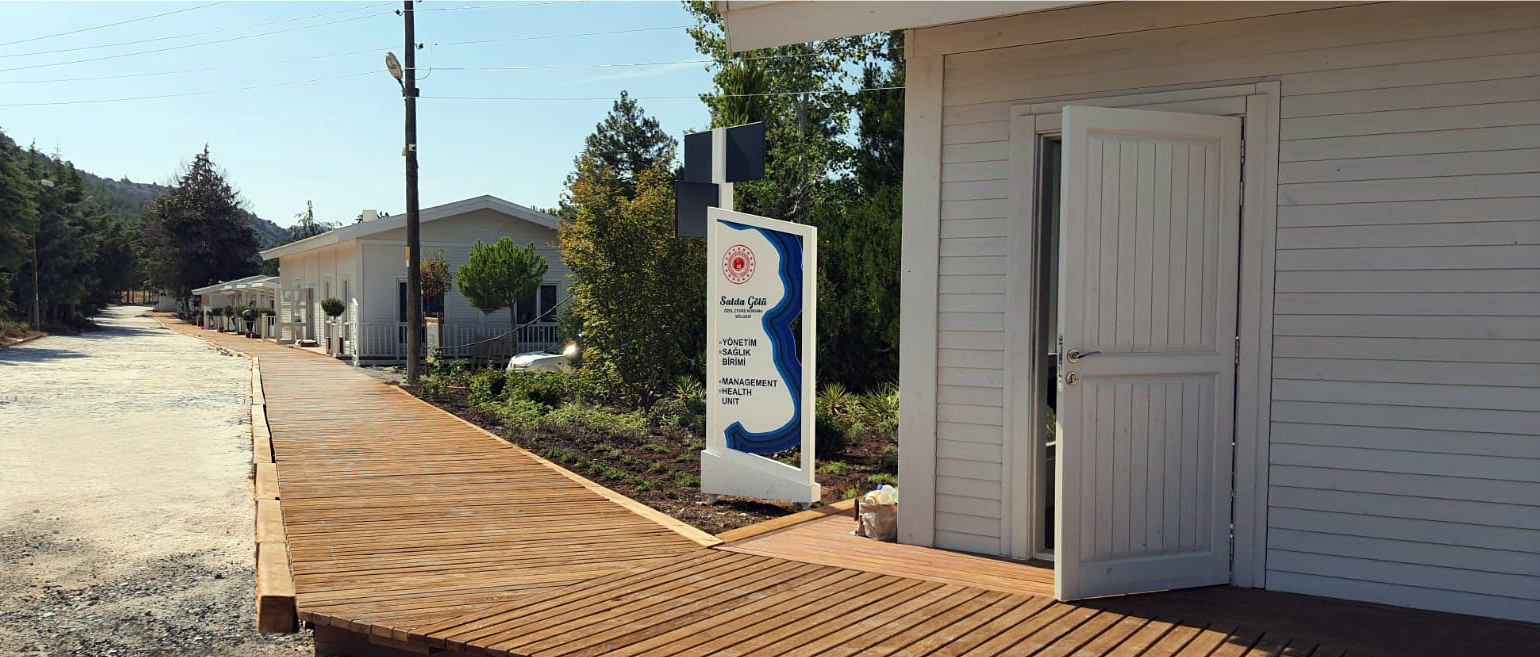
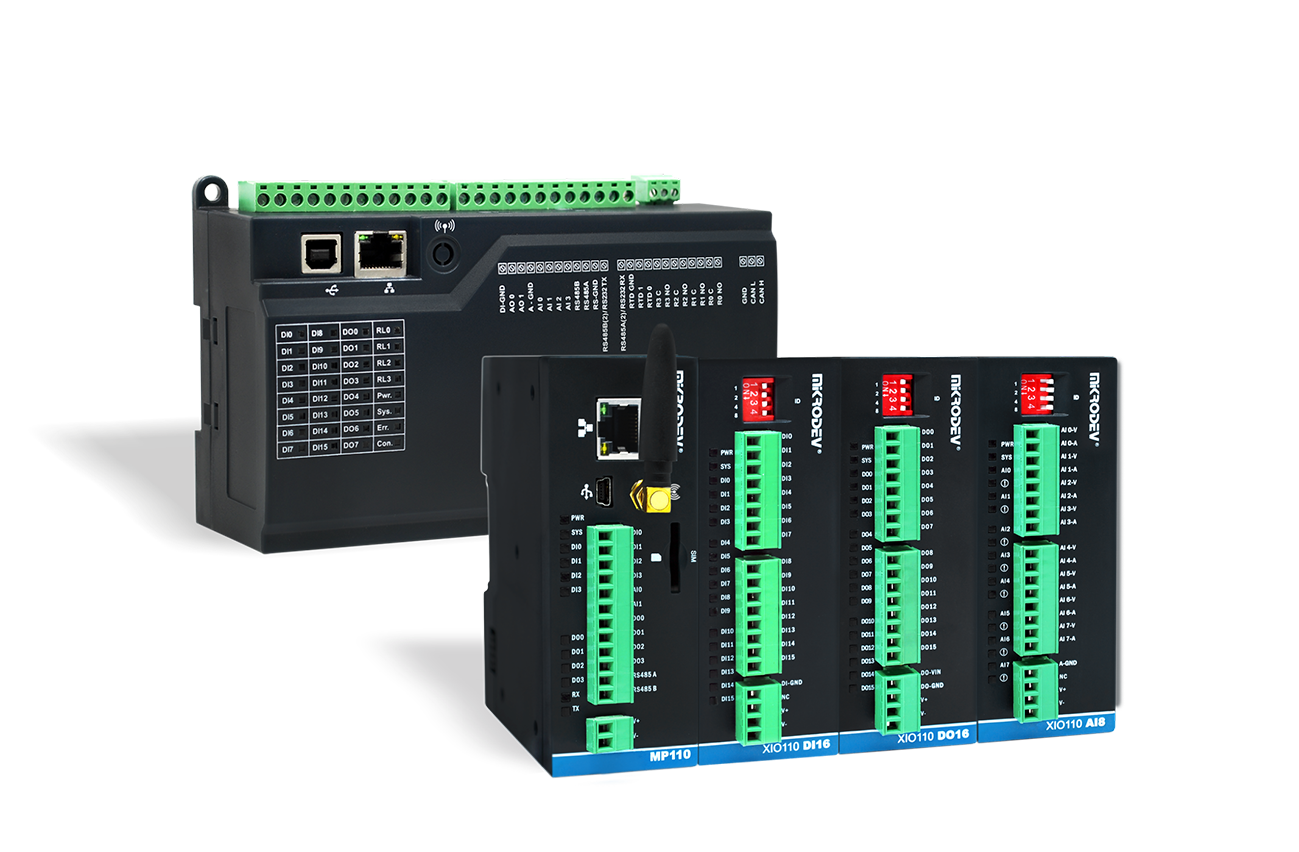
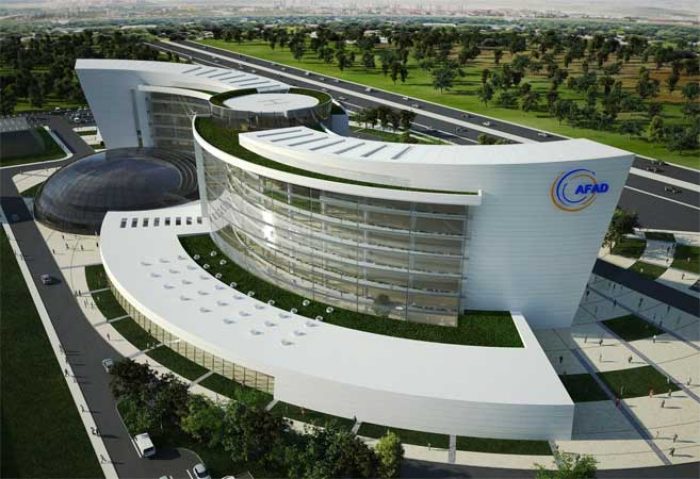
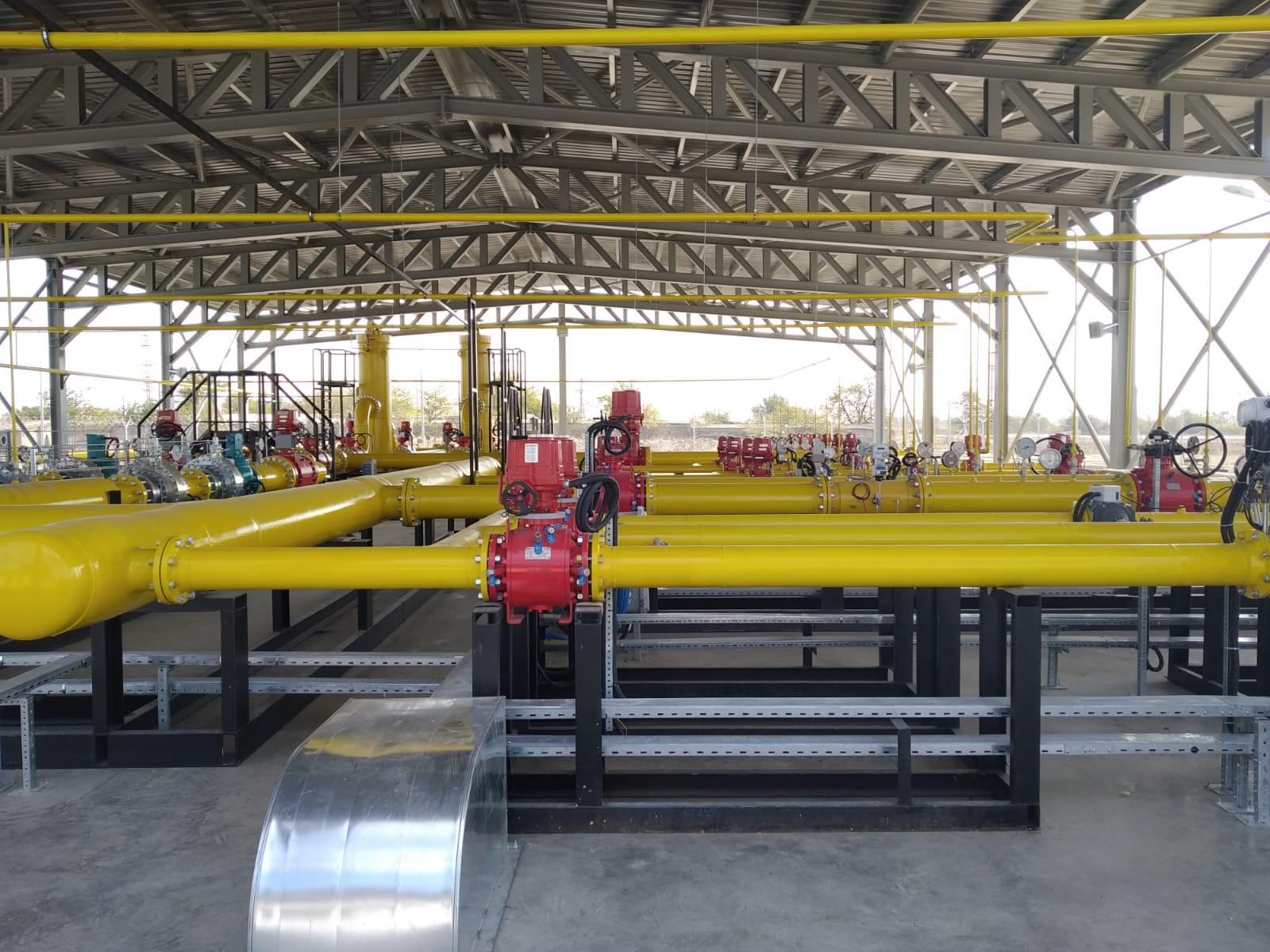