In the realm of industrial automation, Programmable Logic Controllers (PLCs) stand out as crucial automatic control devices, frequently employed in industrial sectors. As we emphasized in our blog post “What is a PLC?“, these devices interact with input and output devices to regulate machines and processes. Data management in PLCs involves the collection, examination, processing, and reporting of data regarding processes controlled by programmable logic control devices. In simpler terms, it encompasses a series of applications and techniques used to ensure that the data stored in the PLC‘s memory is accurate, consistent, and accessible, making data management critically important for the efficient and reliable operation of PLCs.
Common techniques employed for data management in PLCs include:
- Memory Types: PLCs utilize different memory types to store various data. For instance, bit memory is used for input and output values, numeric memory for numerical data, and ASCII memory for textual data.
- Addressing: PLCs assign unique addresses to memory locations, which can be matched with symbolic names used by programmers to access data.
- Access and Modification: PLC programs can access and modify data through data blocks, variables, and functions.
- Security and Protection: PLCs offer various security and protection measures to safeguard data against unauthorized access and modification.
Therefore, data management in PLCs is a critical part of PLC programming and implementation.
PLC programs that effectively utilize data management tend to be more accurate, consistent, and reliable. Data management in PLCs covers aspects such as the types of memory used for data storage, how data is addressed, accessed, and modified, and finally, the security and protection of data.
The advantages of data management in PLCs can be summarized as follows:
- Selective Analysis: Data management aims to select meaningful data among layered data for analysis, enhancing query performance.
- Real-time Access: In PLCs, real-time access to data is crucial, especially in situations requiring quick decision-making.
- Data Integrity: PLC data management ensures data cleanliness, storage, integration, creating a system that provides the fastest and healthiest access to data, backup and recovery systems, and making data analyzable.
- Efficiency, Quality, and Safety: In large enterprises requiring storage, such as in paper, metal, and food processing, PLC data management enhances efficiency, quality, and safety.
How Does Mikrodev Implement Data Management in PLC Devices?
In Mikrodev PLC devices, data management is realized through the device’s integrated data collection capabilities and cloud-based software platform. These devices collect data from sensors, process it, and transfer it to the cloud-based platform.
Data management in Mikrodev’s PLCs generally relies on the device’s hardware and software features. These devices typically collect environmental data through sensors, process this data, and then transfer it to a central data management system via communication protocols. The data collection process involves the steps of sensing, processing, storing, and transmitting the data detected by sensors. This process is usually managed by the device’s microcontroller or embedded software. Consequently, Mikrodev devices can collect, process, and transmit data to a central data management system.
Data management in Mikrodev PLCs is often implemented through special software and hardware modules. The PLC programming and data management in Mikrodev’s MP110 Series PLC (Micro Level Controller) and MP211 Series PLC (Medium and Large Level Controller) devices, as mentioned in our previous articles, are used in industrial automation and control systems. Mikrodev PLC devices are typically compatible with various sensors, such as temperature, pressure, humidity, current, and voltage sensors, commonly used in industrial environments. These native PLCs by Mikrodev are designed to adapt to a wide range of industrial applications.
If you found this article intriguing, we recommend checking out our blog content on “FAQs (Frequently Asked Questions) About PLC,” “MODBUS TCP Protocols and Applications in Mikrodev PLC Devices,”, “What is PLC Programming? MOBDUS RTU Protocols in Mikrodev PLC Programming”, “Increasing Efficiency: Using MODBUS Gateway in PLC Programming”, How to Reduce Maintenance Costs with Aging Functions iN PLC Programming ?”, “What are the Differences Between PLC and RTU?” and “IEC 61131-3 Programming and Its Relation to the PLC Devices”.
Mikrodev, a leading brand among PLC manufacturers, offers programmable logic control devices that are utilized in various sectors from building automation to energy systems, water systems to process automation, machine automation to transportation systems, IoT, telemetry applications, lighting systems, and agriculture irrigation systems. These products, by enabling savings between systems, have the potential to enhance efficiency.
Thanks to these unique features, Mikrodev products stand out in the industrial automation sector with their native product solutions and are preferred in various application areas.
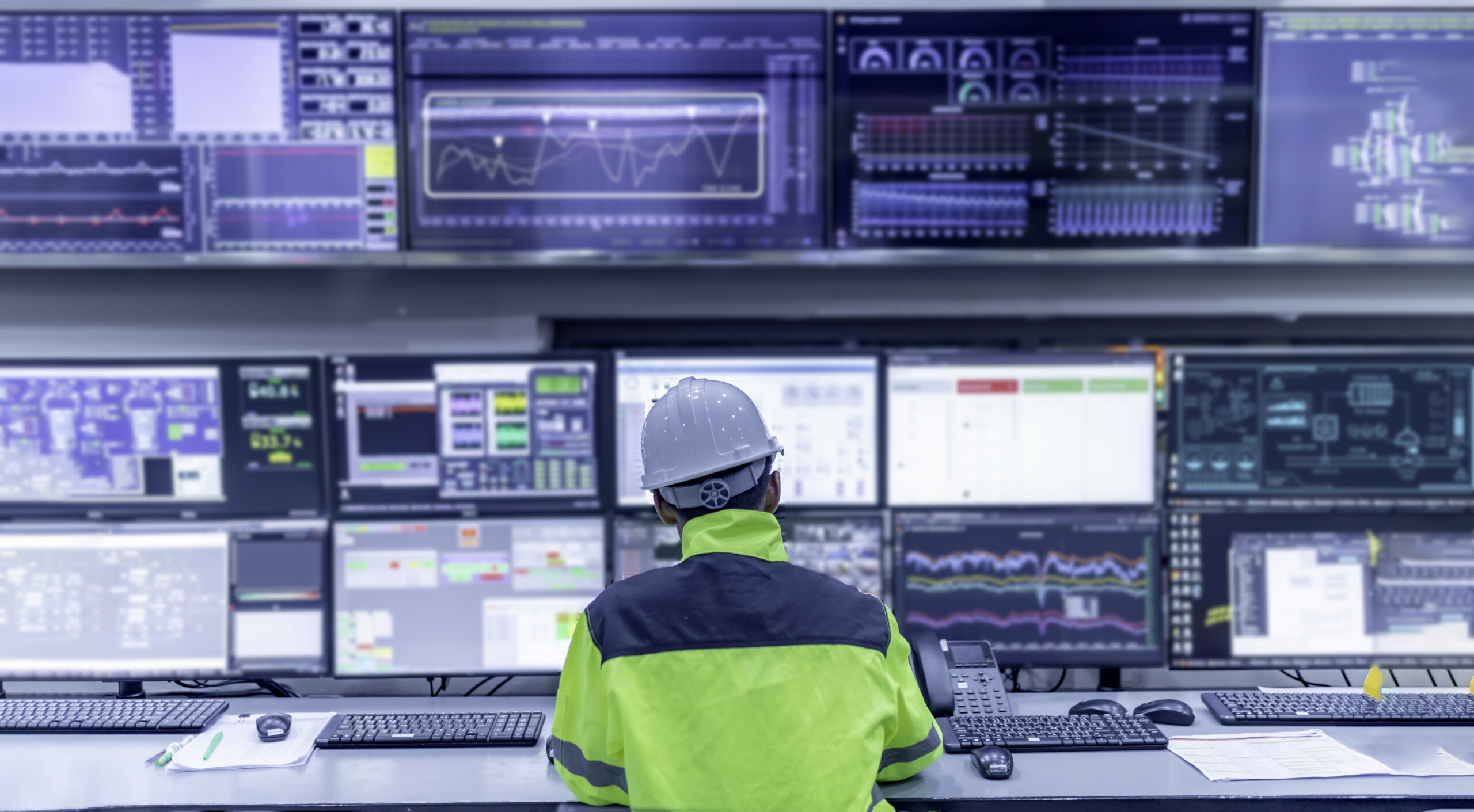
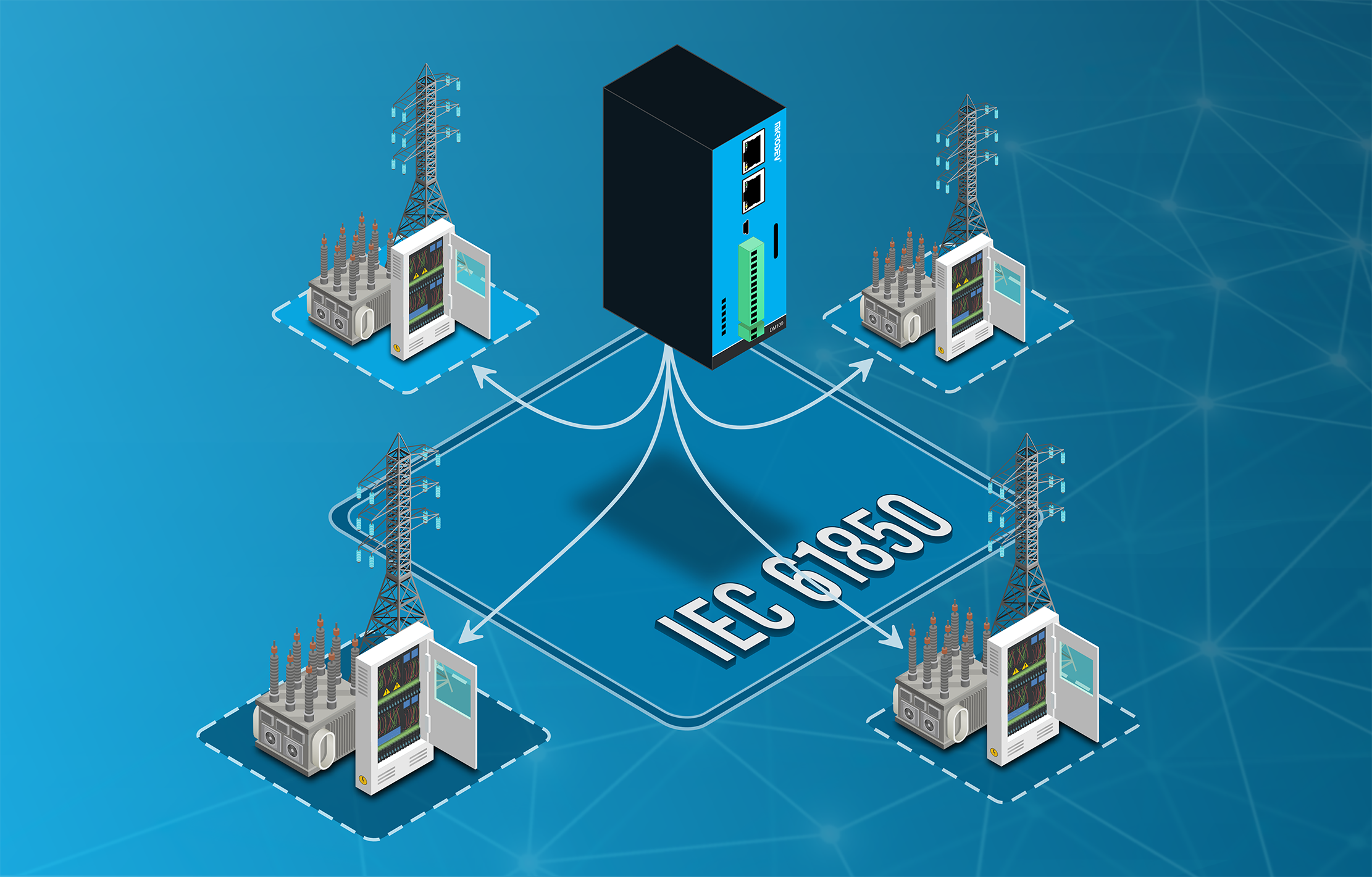
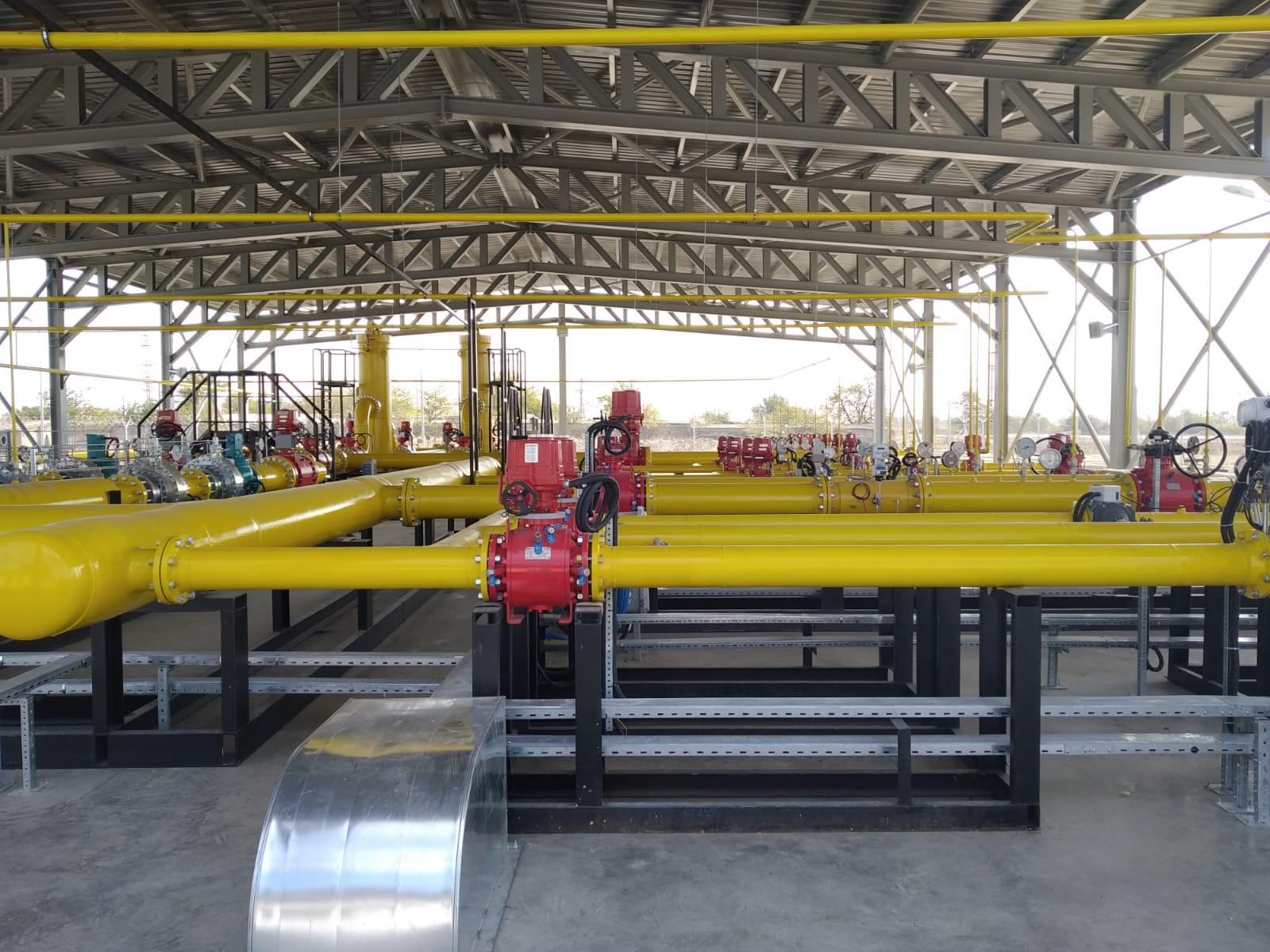
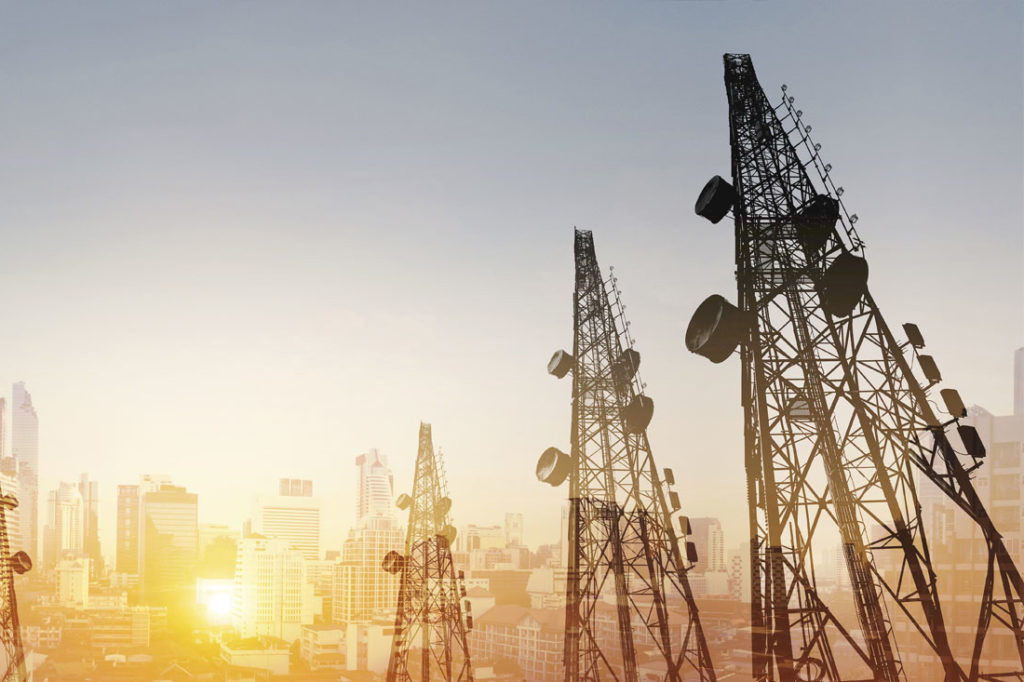
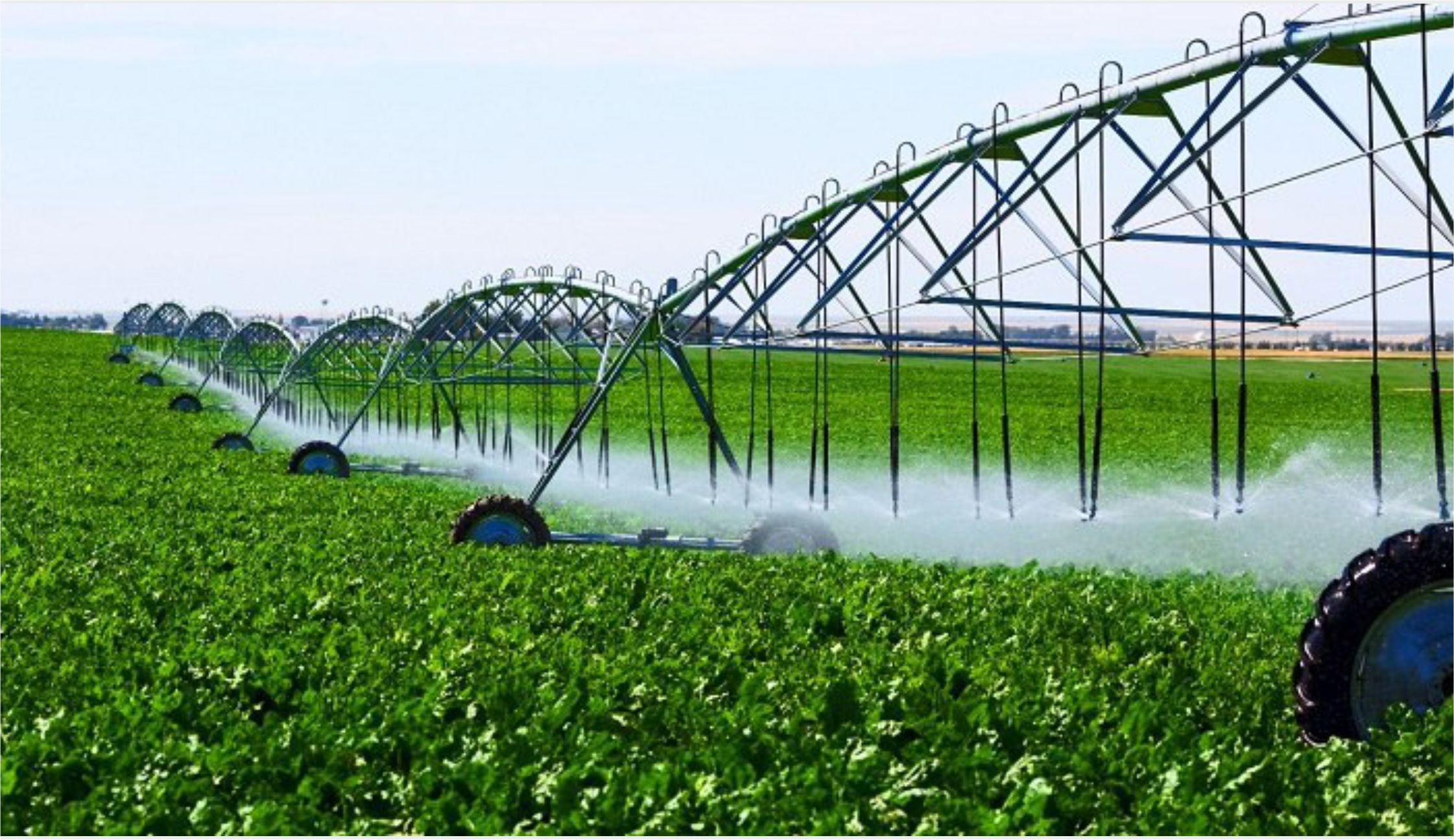
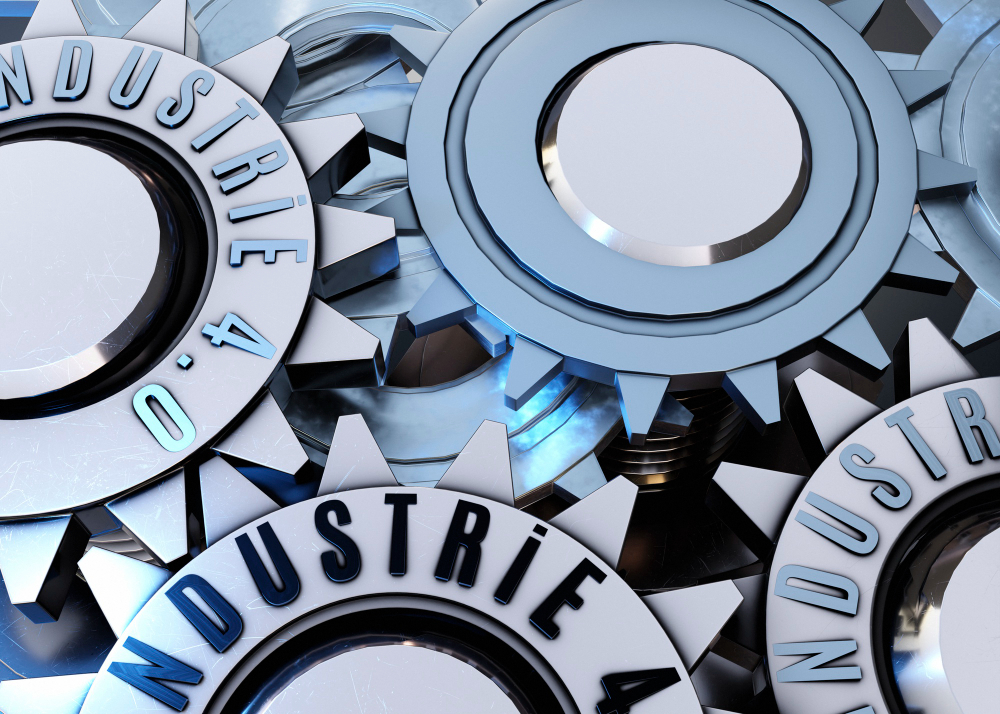
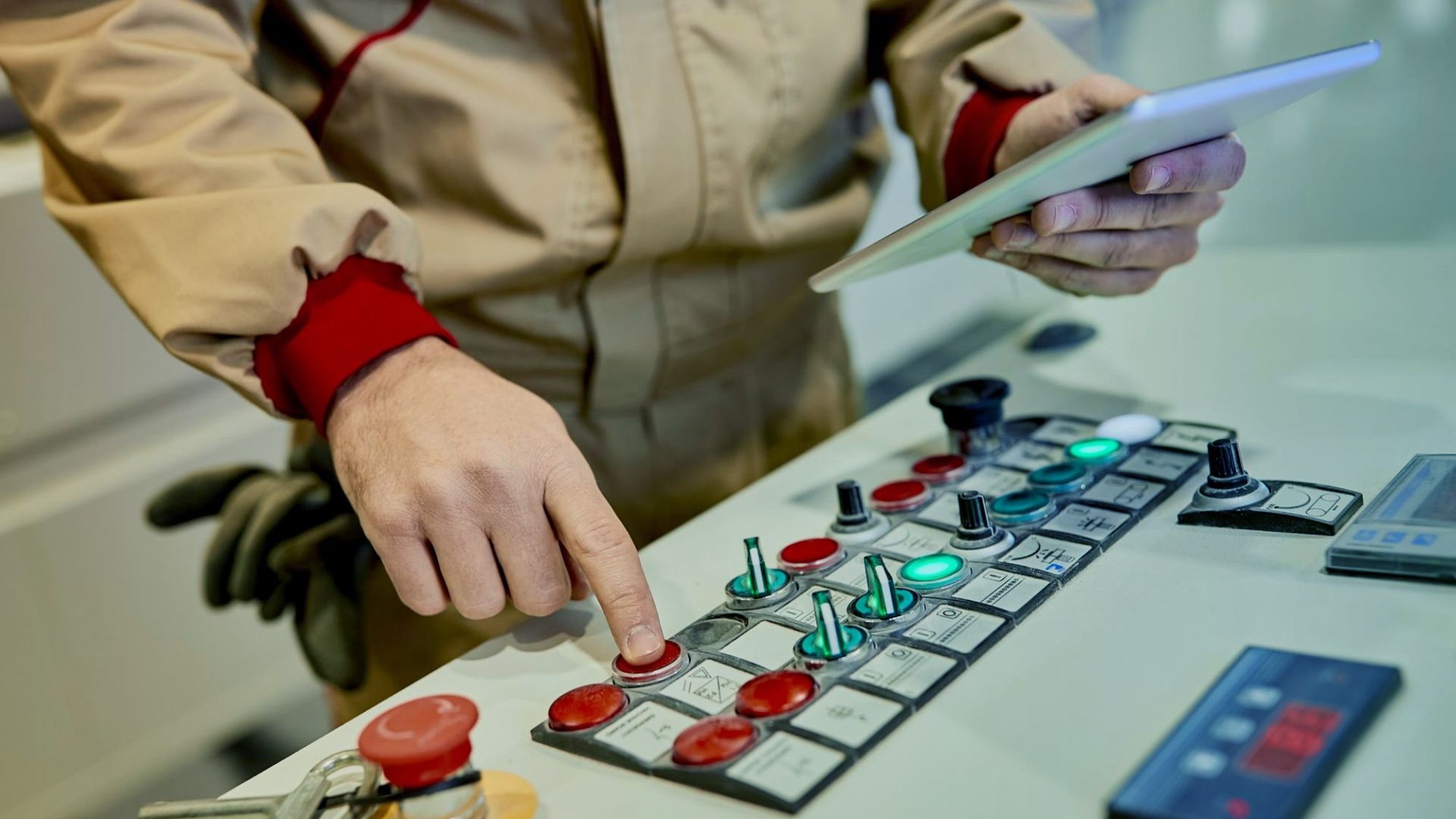
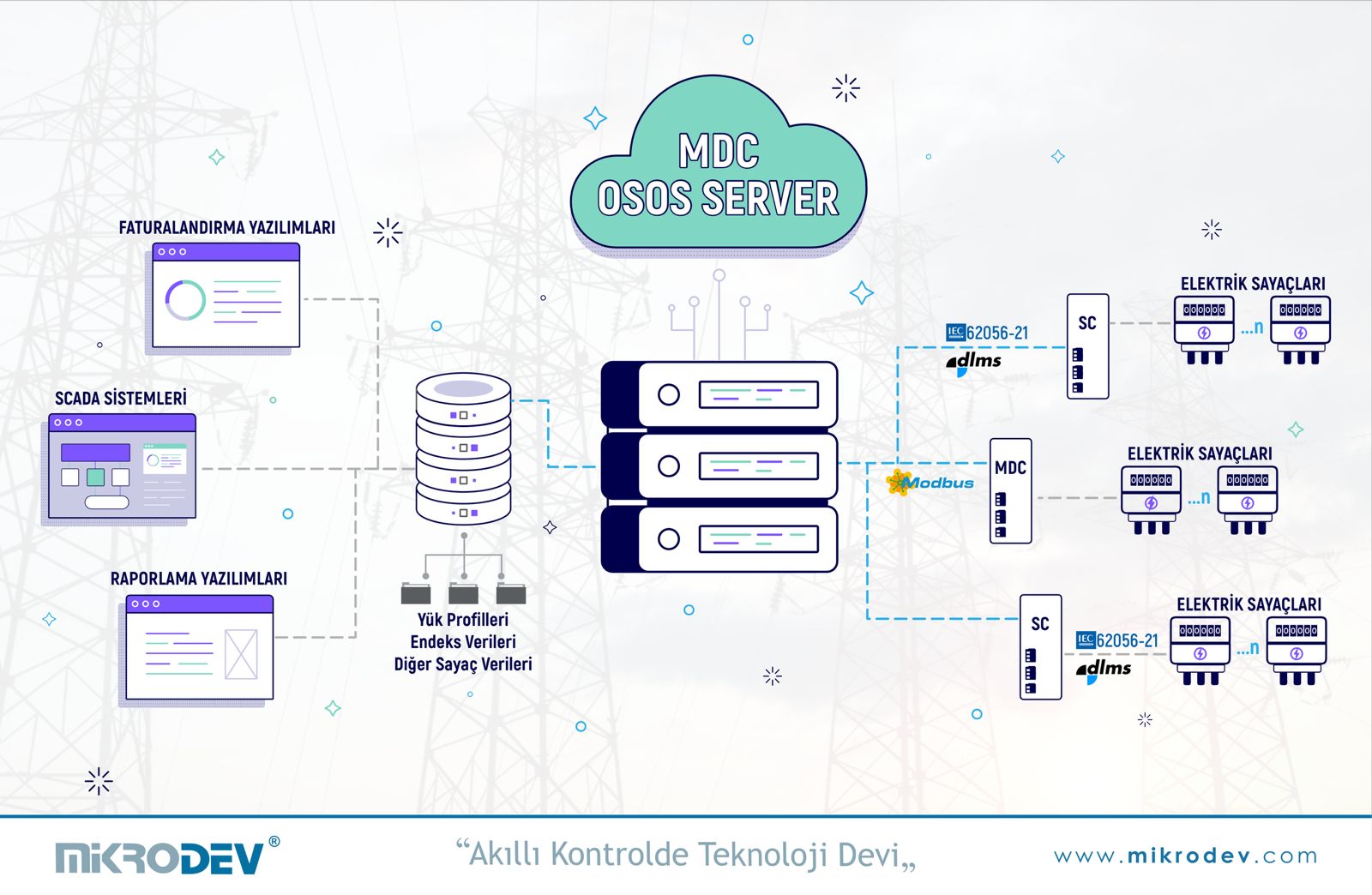
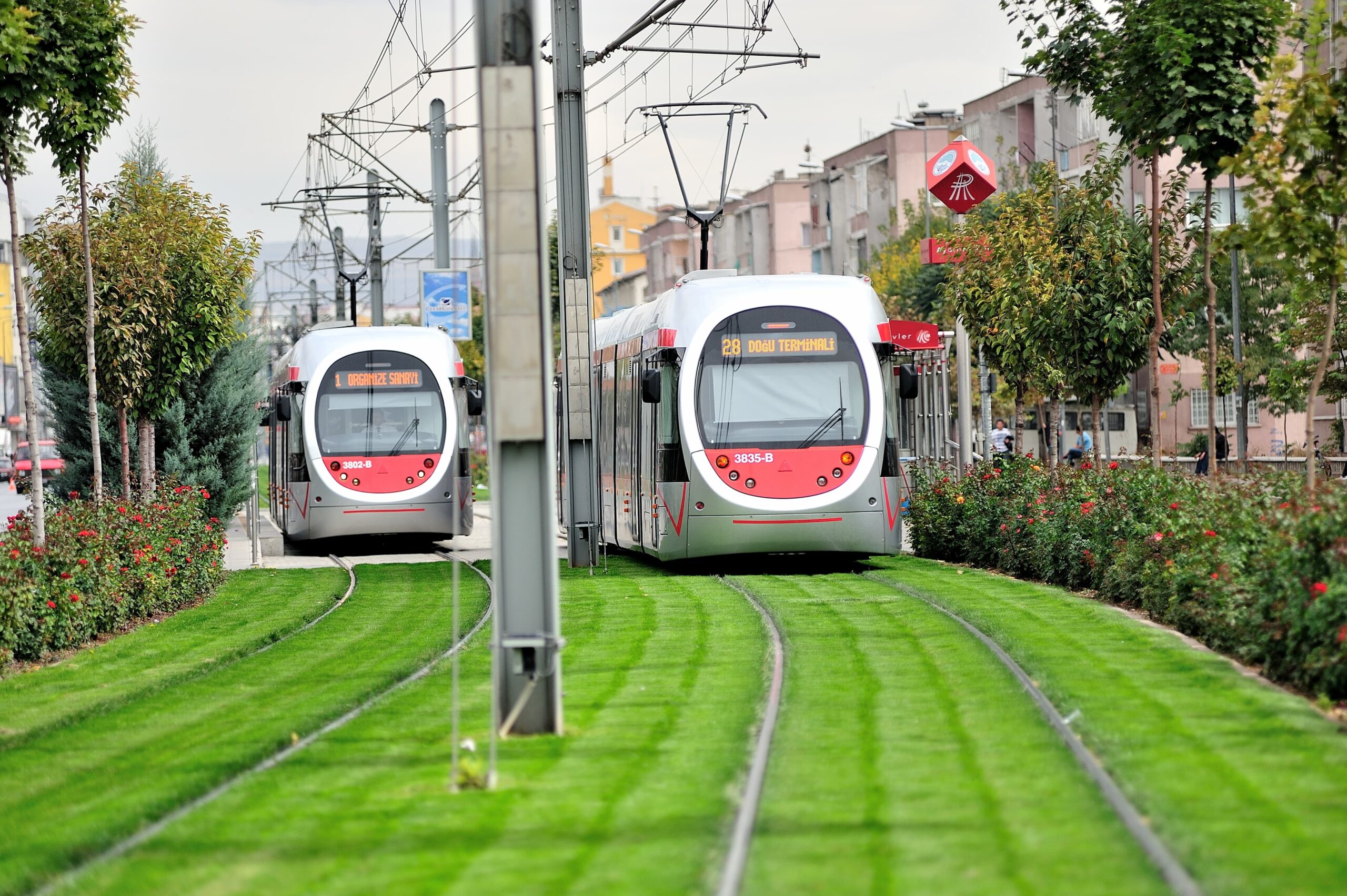
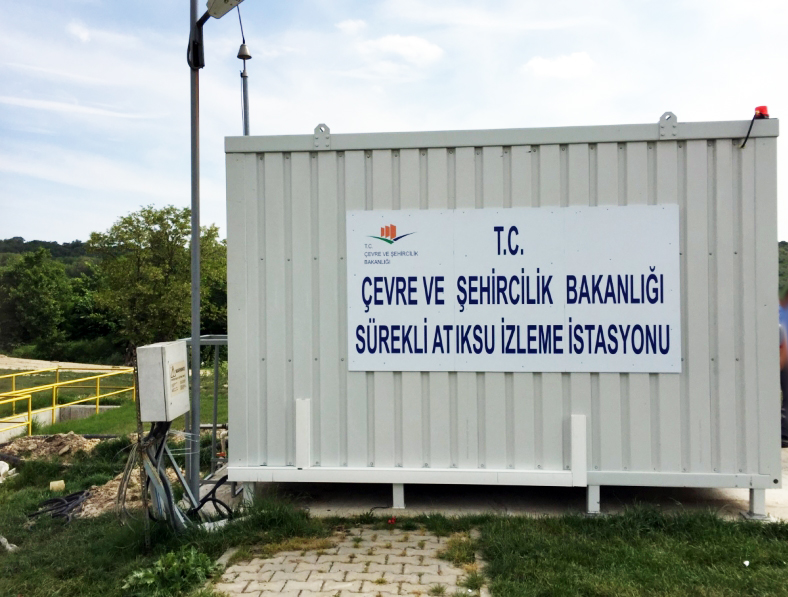