Programmable Logic Controllers (PLCs) are widely used in the industrial automation industry to control and monitor various processes. One of the main functions of PLCs is motion control, which involves precise control of motors, actuators and other mechanical devices. In this article, we will cover the basics of motion control with PLC, the components involved in this process, the required PLC programming techniques and real application examples on Mikrodev PLC devices.
Introduction to PLC
As we have mentioned in many of our guides and blogs, especially in “What is PLC?” blog on our website, PLC (Programmable Logic Controller) is a control device used in industrial automation systems. PLC devices can be programmed with a method called plc programming and can control machines and processes by communicating with various plc input and output elements. In this context, PLC can also be defined as an automation device supported by plc software.
Motion control is an automation application used to direct the motion of a mechanical system in a desired way. Motion control is realized by devices called plc drivers and plc plays a crucial role in automation systems. The PLC driver acts as an interface between plc input and output elements and controls moving elements such as motors, servos, stepper motors according to the commands specified by the plc program.
What is Motion Control and Why is it Essential?
Motion control refers to the ability of a PLC device to monitor and control the precise and controlled movement of mechanical components, especially motors, actuators and carriers. This plays an important role in industrial automation because it ensures efficiency, accuracy and safety in various production processes.
When motion control is implemented with PLC devices, manufacturers can achieve synchronized and coordinated movement of machines, which means precise positioning, speed and torque control. This level of control can significantly increase productivity, reduce processing times and optimize energy use.
Motion control also has a critical role in performing complex tasks such as robotics, packaging, CNC machining and material handling. Using different motion control techniques, such as trajectory planning, speed profiles and digital position control, PLC devices can accurately perform these tasks and meet the required specifications.
Understanding PLC Devices and their Role in Motion Control
We have already mentioned that PLC devices are electronic devices that are widely used in industrial automation to control and monitor various processes. These devices receive input signals from sensors and switches, process them according to the predefined program and then generate output signals to control motors, actuators and other devices.
When it comes to motion control, PLC devices function as a critical part of the overall system. They receive information from sensors about motion parameters such as speed, position and acceleration, and then calculate and generate the appropriate control signals using the program.
One of the main advantages of using PLC devices for motion control is their ability to handle complex logic and perform fast calculations. This allows real-time monitoring and adjustment of motion parameters, thus ensuring precise and accurate control.
Furthermore, PLC devices can also provide advanced functionality such as motion synchronization, trajectory planning and error correction. These features provide manufacturers with the ability to achieve synchronized and coordinated motion of multiple machines, which in turn supports the efficiency and productivity of the systems.
To implement motion control with PLC devices, it is important to select the right PLC hardware and software, properly configure and program the device.
Step by Step: How to Implement Motion Control with PLC Devices
In this section, we will provide a step-by-step guide on how to implement motion control with PLC devices. By following these steps, you will be able to effectively implement motion control in your industrial automation system.
Step 1: Choose the Right PLC Hardware
The first step is to choose a PLC hardware that suits your motion control needs. You can select the right hardware by taking into account factors such as the number of input/output points, communication capabilities, processing power and compatibility with your existing system. It is critical to choose a PLC device that can effectively manage the complexity and performance demands of motion control.
Step 2: Install and Configure the PLC Device
After selecting the PLC hardware, you can proceed to the device installation and configuration phase. Correctly assemble your PLC device according to the instructions of the local PLC manufacturer Mikrodev. Then install sensors, switches, motors and other components.
Step 3: Develop a Motion Control Program
Programming is a critical step in motion control. Depending on your specific motion control requirements, develop a motion control program using a programming language such as ladder logic or structured text. Define the logic for calculating motion parameters, controlling motors and monitoring motion feedback signals.
Step 4: Test and Validate the Program
It is essential to test and validate the program before commissioning the motion control system. Use simulation tools or a test environment to ensure that the program works as intended. Test different scenarios and make sure that the PLC device controls the motion parameters correctly.
Step 5: Adjust and Optimize the Motion Control System
Once the program is confirmed, adjust and optimize the motion control system. Make adjustments to improve the accuracy, speed and synchronization of the motion. Analyze the performance of the system, identify potential areas for improvement and make the necessary adjustments to optimize the motion control functionality.
By following these steps, you can effectively realize motion control with PLC devices.
If you demand to learn more technical details about PLC, i.e. programmable logic controllers, we advise other technical blog posts on the subject such as “MODBUS TCP Protocols and Applications in Mikrodev PLC Devices“, “What is Data Management in PLC, What are the Advantages?“, “Increasing Efficiency: Using MODBUS Gateway in PLC Programming“, “Importance of Calendar and Timing Functions and PLC Programming”, “What are the Differences Between PLC and RTU?”, “How to Reduce Maintenance Costs with Aging Functions in PLC Programming?”and “FAQs (Frequently Asked Questions) About PLC” that will help you to find solutions to your questions about PLC and explain these solutions through Mikrodev devices.
Motion Control Application Examples in Microdev PLC Devices
Mikrodev, Turkey’s primary plc manufacturer in the automation industry, has carried out many successful projects in the field of industrial automation with its plc products. A few examples of applications in the field of Mikrodev PLC devices, including motion control, can be listed as follows:
Aramco Emergency Shutdown System (ESD): Saudi Arabia’s oil company Aramco, which is among the top three most valuable companies in the world, has preferred MP211 Series Mikrodev PLC products for the Emergency Shutdown System controls of its facilities located in more than 50 stations. This system ensures safe shutdown of the facilities in case of emergencies such as fire, leakage, explosion, etc. Mikrodev PLCs monitor the status of the plants, give alarms and make necessary interventions.
Arçelik Control Test System: In order to improve the quality of the remote controls of the televisions produced for ARÇELİK, a powerful manufacturer of white goods and durable home appliances in the global market, a 3-axis motion test system was developed using MP110 series Mikrodev PLC and Viewsmart Mikrodev SCADA products. With the developed motion control system, the performance outputs of the remote control at different distances and angles can be continuously recorded.
In our Linkedin post below, you can watch the details of the Arçelik Remote Control Test System project. Linkedin post:
Mikrodev, the sectoral leader of production PLC brands in Türkiye, continues to meticulously produce automation products that serve many various areas of industrial automation and today’s smart technologies. Mikrodev programmable logic controller products, addressing many divergent fields such as smart building automation, energy systems, water systems, process automation, machine automation, transportation systems, IoT and telemetry applications, lighting systems and agricultural irrigation systems, offer savings to institutions, companies and facilities by providing efficiency between demands and resources. You can contact our experts to get information about Mikrodev solutions.
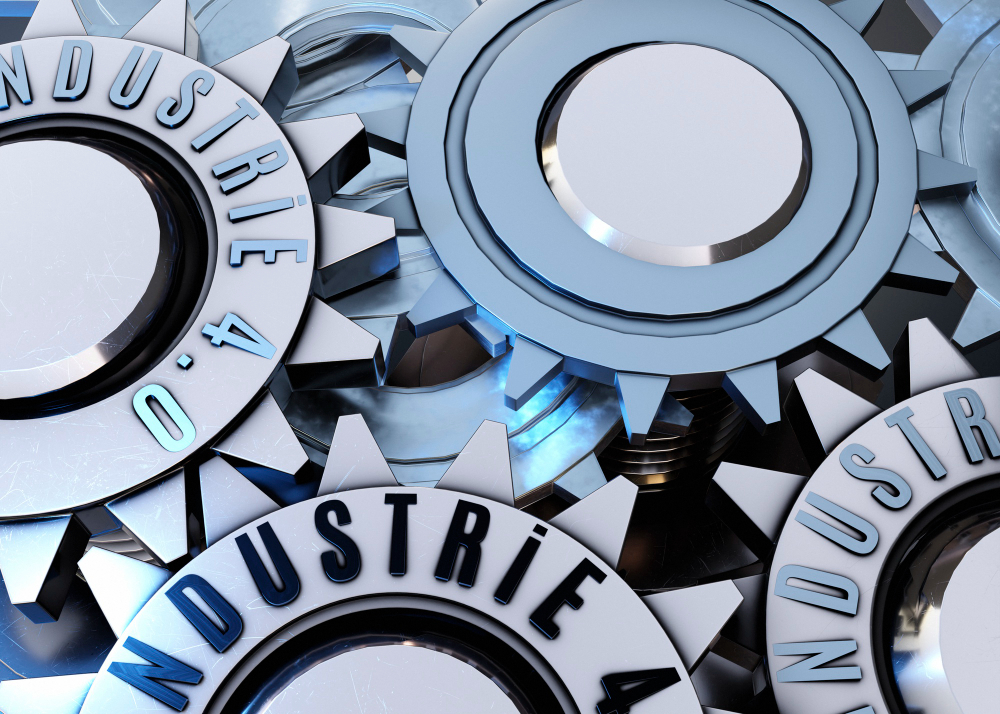
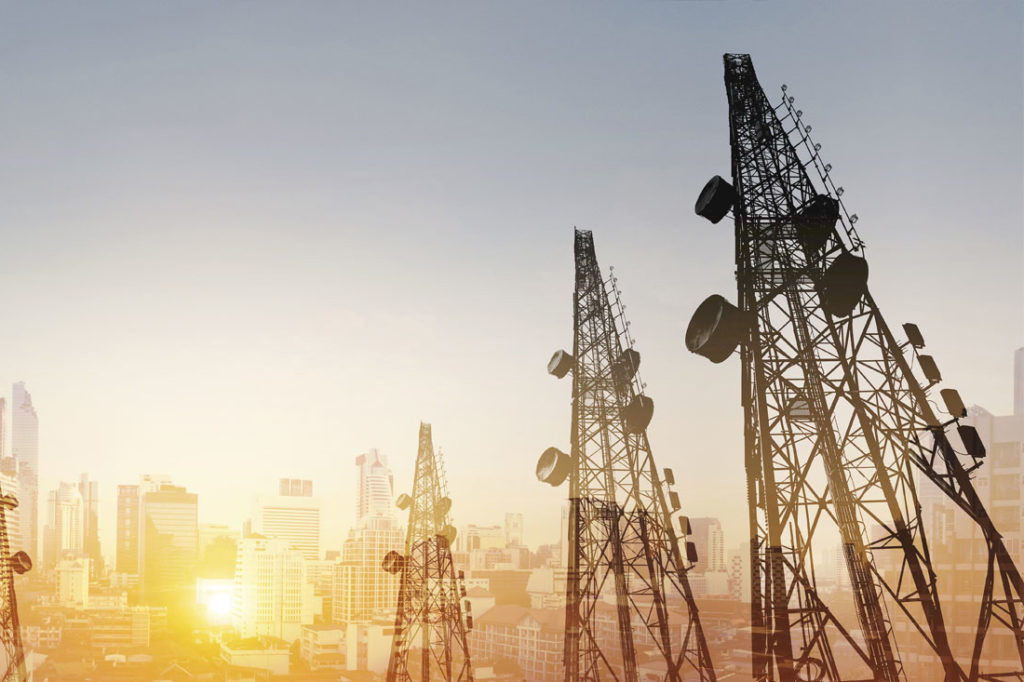

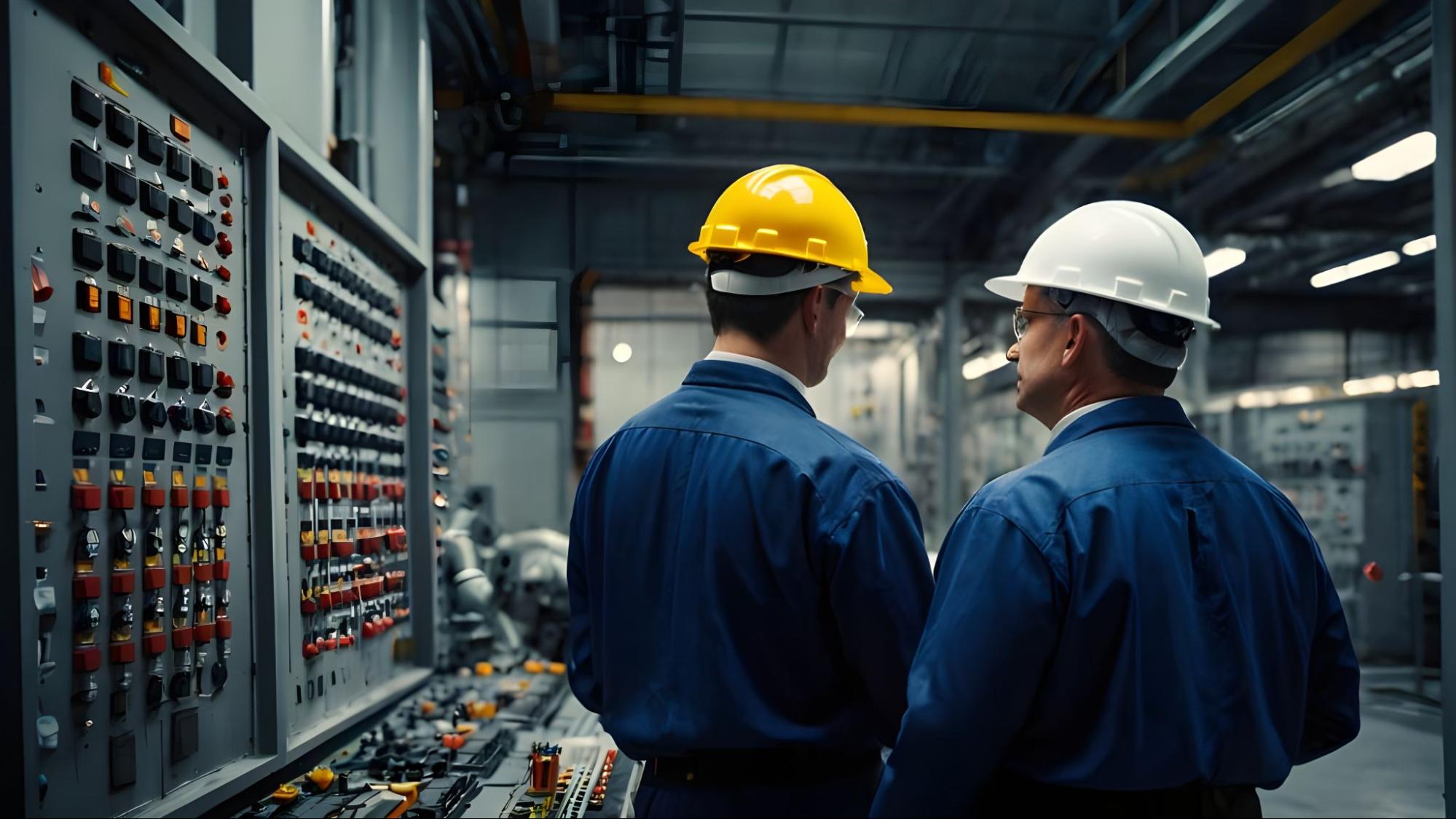
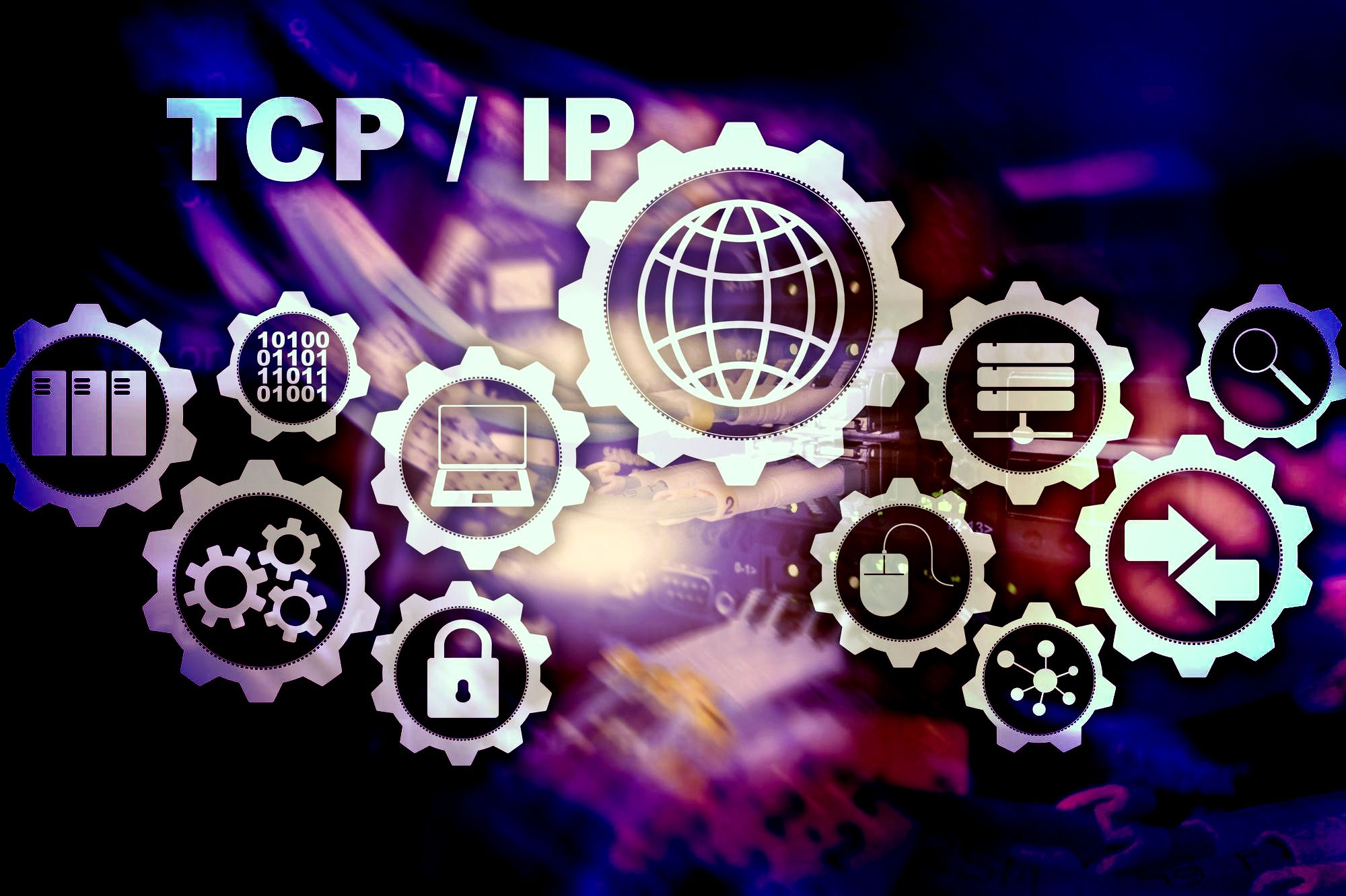
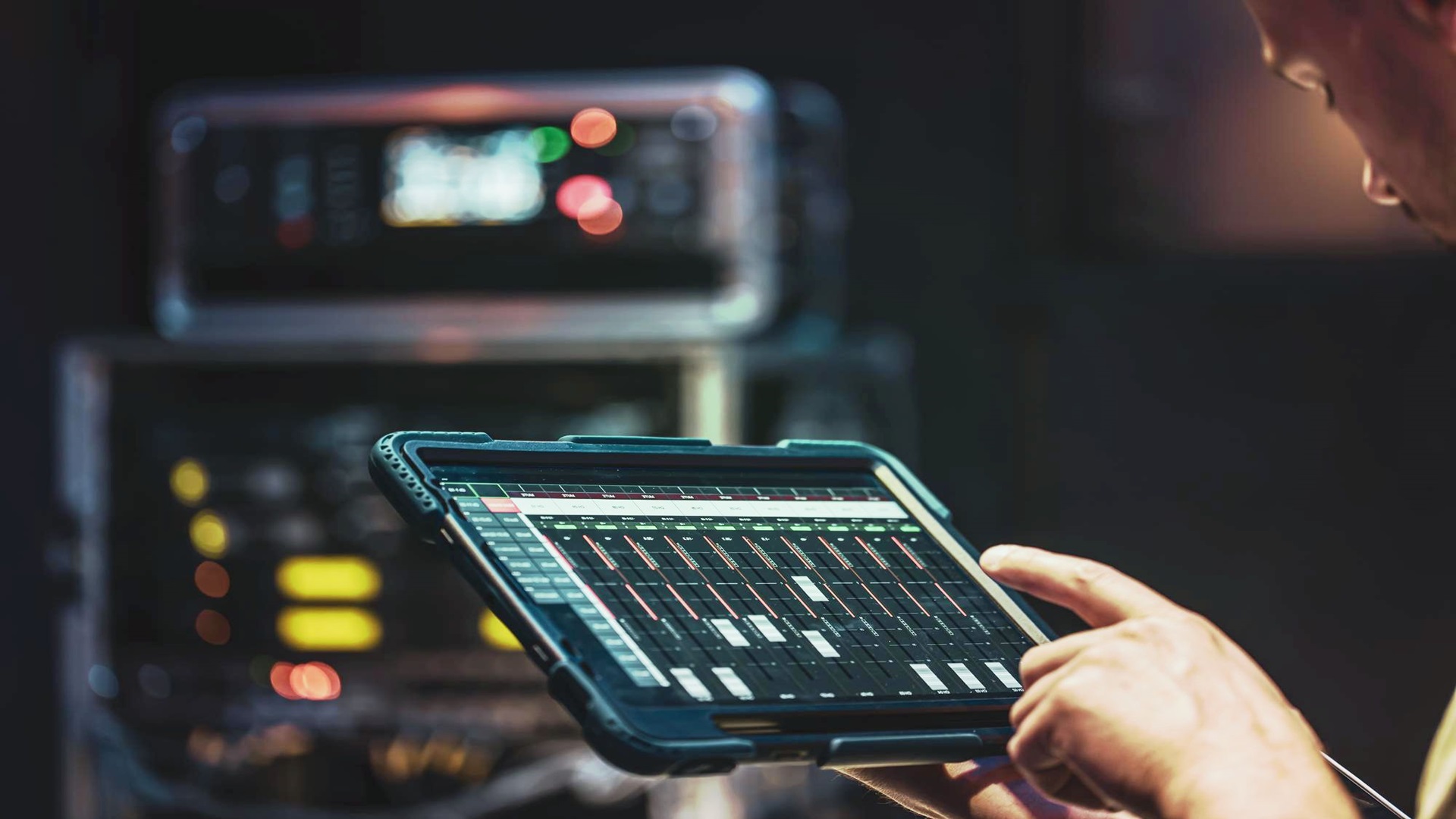
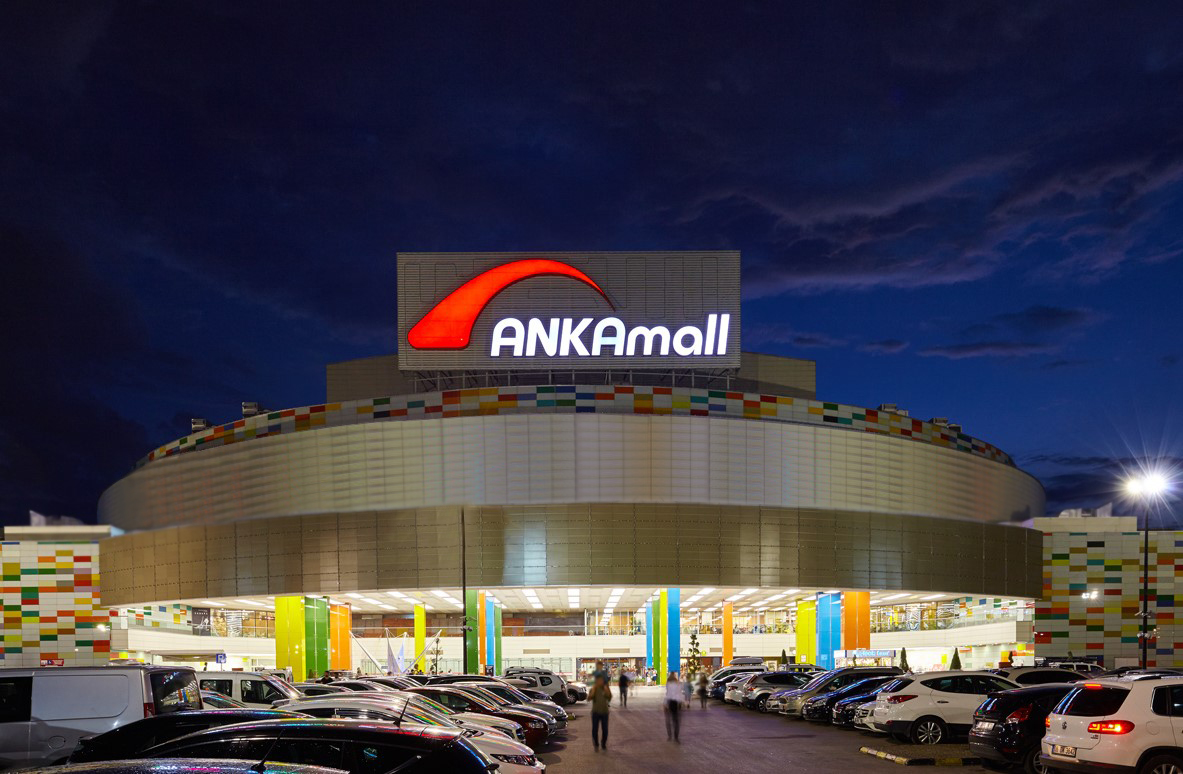
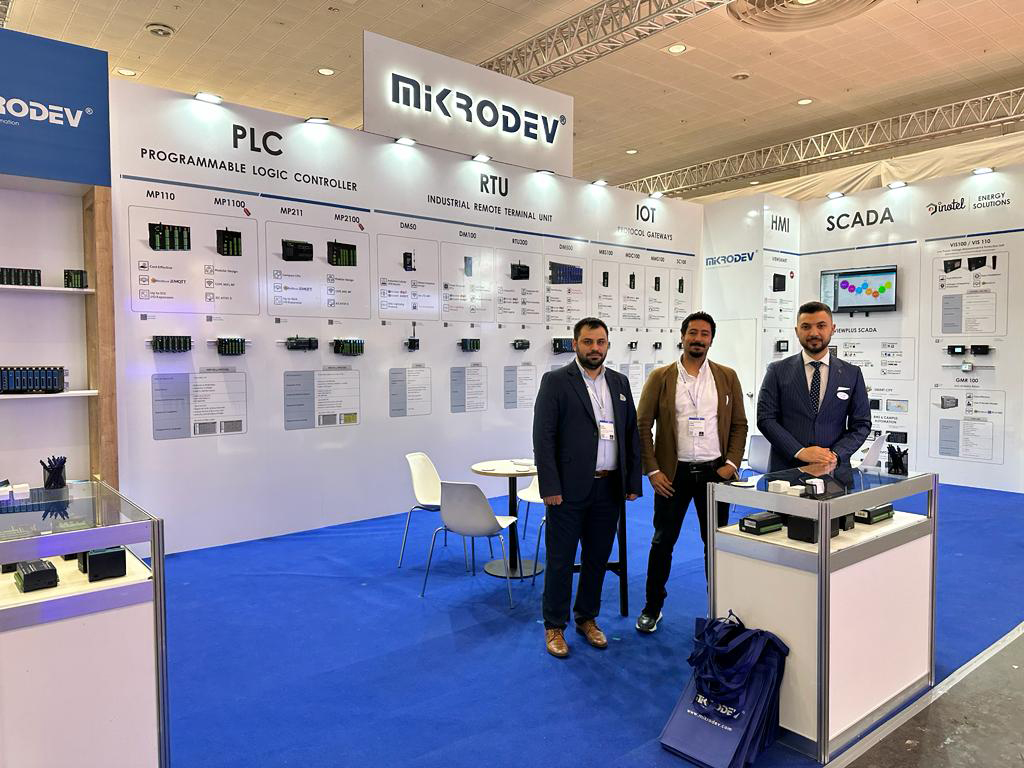
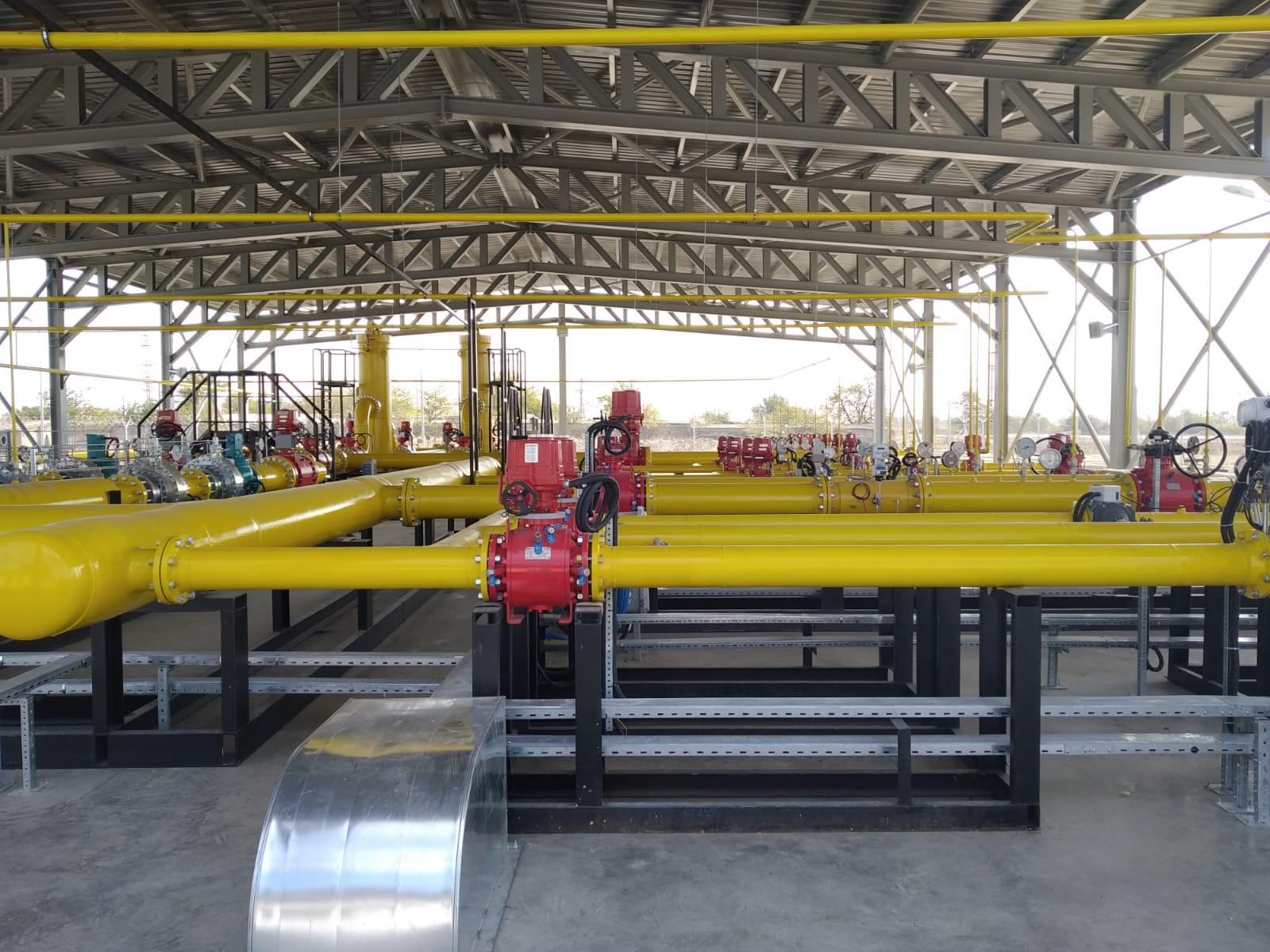
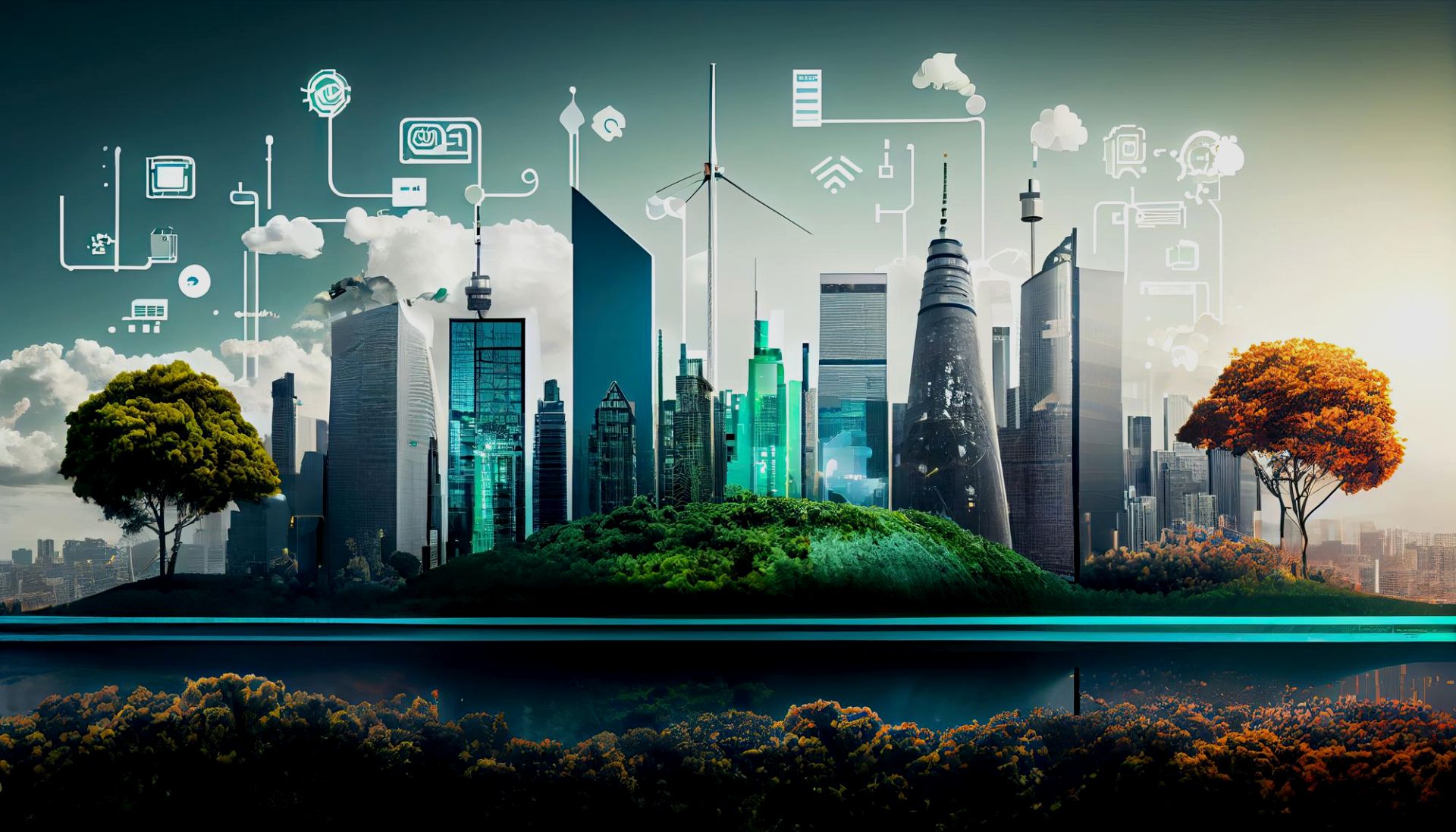