In the world of industrial automation, PLC (Programmable Logic Control) and RTU (Remote Terminal Unit) are two substantial devices. They are both used to automate and monitor process control, however, there are some essential differences between them. In this article, we will explore the differences between PLC and RTU and which device is more suitable for which specific industrial application.
Basics of PLCs and RTUs
Before getting into the basic differences between PLC and RTU, it is important to understand what both devices are and how they work.
PLC (Programmable Logic Controller): PLCs are microprocessor-based controllers and are often thought of as the workhorses of industrial automation. They are used to automating and monitoring complex processes. PLCs are programmed to control a process, and this program loops within a certain period. Therefore, they cannot detect signal changes within a given period.
RTU (Remote Terminal Unit): RTUs are parameter-based devices. These devices detect all signals in the correct time frame and record them with time information. RTUs do not cause signal loss and are generally preferred in applications that require precise control. For example, they can quickly detect power outages and activate backup power supplies.
What are the Differences Between PLC and RTU?
- Programming Language: PLCs and RTUs use different programming languages. While PLCs are usually programmed with ladder logic, RTUs use platforms based more on configuration. This means that the programming processes of both devices are different. Mikrodev manufactures RTU products that can be programmed like a PLC, which is different from the traditional conception.
- Feedback and Processing: Both devices are used to control inputs, monitor equipment, and send alarms to a central unit. However, RTUs perform basic calculations by reading one sensor signal at a time and performing multiple iterations and loop actions in a program scan. PLCs, on the other hand, can be programmed to read multiple inputs simultaneously, process much more complex calculations, and make decisions based on these inputs.
- Communication Protocol: The main difference between RTUs and PLCs is their communication protocols. RTUs are mostly preferred in distributed SCADA systems. For this reason, RTUs are preferred in systems where data security and reliability are sensitive, since going to the field in case of possible errors or malfunctions in distributed structures increases operational costs. They have communication standards developed according to this need, such as DNP3, IEC61850, IEC60870-5-104, IEC60870-5-101, IEC60870-5-101, MQTT. PLCs are preferred to be used within a certain location. Therefore, they do not need the above communication protocols. Speed is the most important preference in the communication of PLC products. For this reason, communication protocols such as MODBUS, PROFIBUS, PROFINET, ETHERNET IP, ETHERCAT, and BACNET are generally preferred by PLCs.
Check Mikrodev’s RTU ve PLC Products Now!
You can review the technical details of Mikrodev’s RTU and PLC> products on our product pages! Mikrodev
RTU‘s, which are an excellent choice for applications requiring precise control and fast signal processing, offer high quality, reliability and performance.Contact our experts nowfor customized solutions for your projects and take the step towards success by choosing the right RTU device!
Cost Differences Between PLC and RTU Devices
The cost of RTUs and PLCs depends on the intended use and the number of inputs they can control. PLCs generally offer more functionality, so they can be more expensive than RTUs in systems with complex programming needs. However, in systems where there is a need for high data security and reliability, RTUs can offer a more cost-effective solution.
PLC or RTU? Which Device Should You Choose?
Which device you choose depends on the requirements of your project actually. If you need to perform complex tasks and have additional programming knowledge, PLCs may be more suitable. But for simpler tasks and applications that require precise control, RTUs may be a better option.
In conclusion, PLC and RTU play crucial functions in the world of industrial automation. The architecture, programming language, and responses to feedback signals are different. Therefore, you should choose which device is more convenient for you, considering the requirements and budget of your project.
Mikrodev RTU and PLC Products: The Solution for Your Needs
In industrial process control, choosing the right device can greatly simplify your work. As Mikrodev, we offer our customers excellent solutions for both RTU and PLC needs. Mikrodev’s RTU products are an excellent choice for applications that require precise control and fast signal processing. Also, our PLC products are designed for your industrial automation projects with the ability to handle complex tasks. Both products offer high quality, reliability, and performance. By working with Mikrodev, you can secure your decision to choose the right device for the success of your industrial automation projects. Contact our experts today to learn more about custom solutions for your projects.
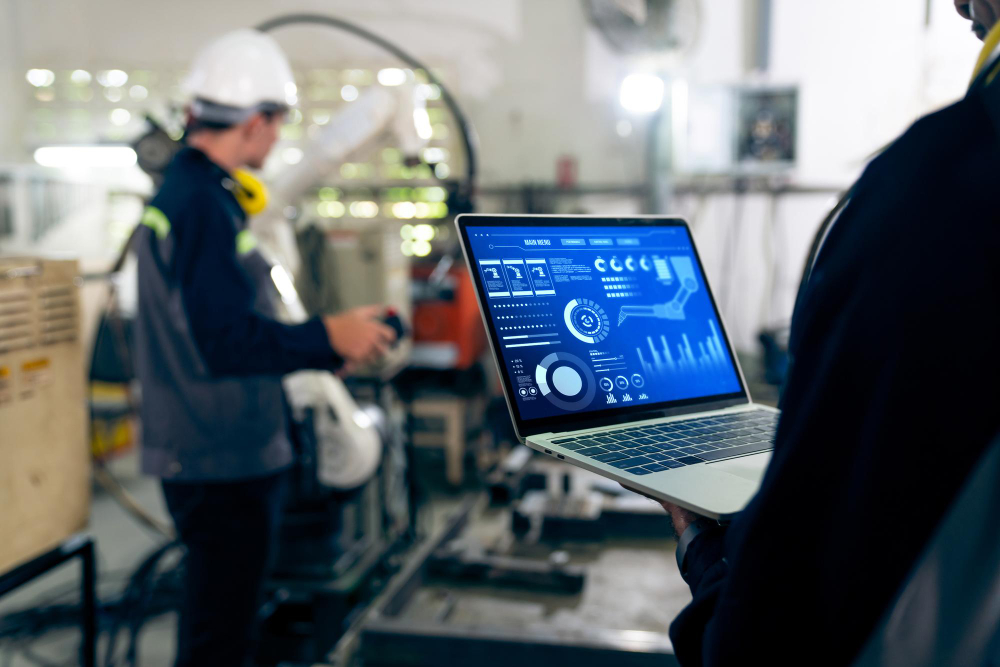
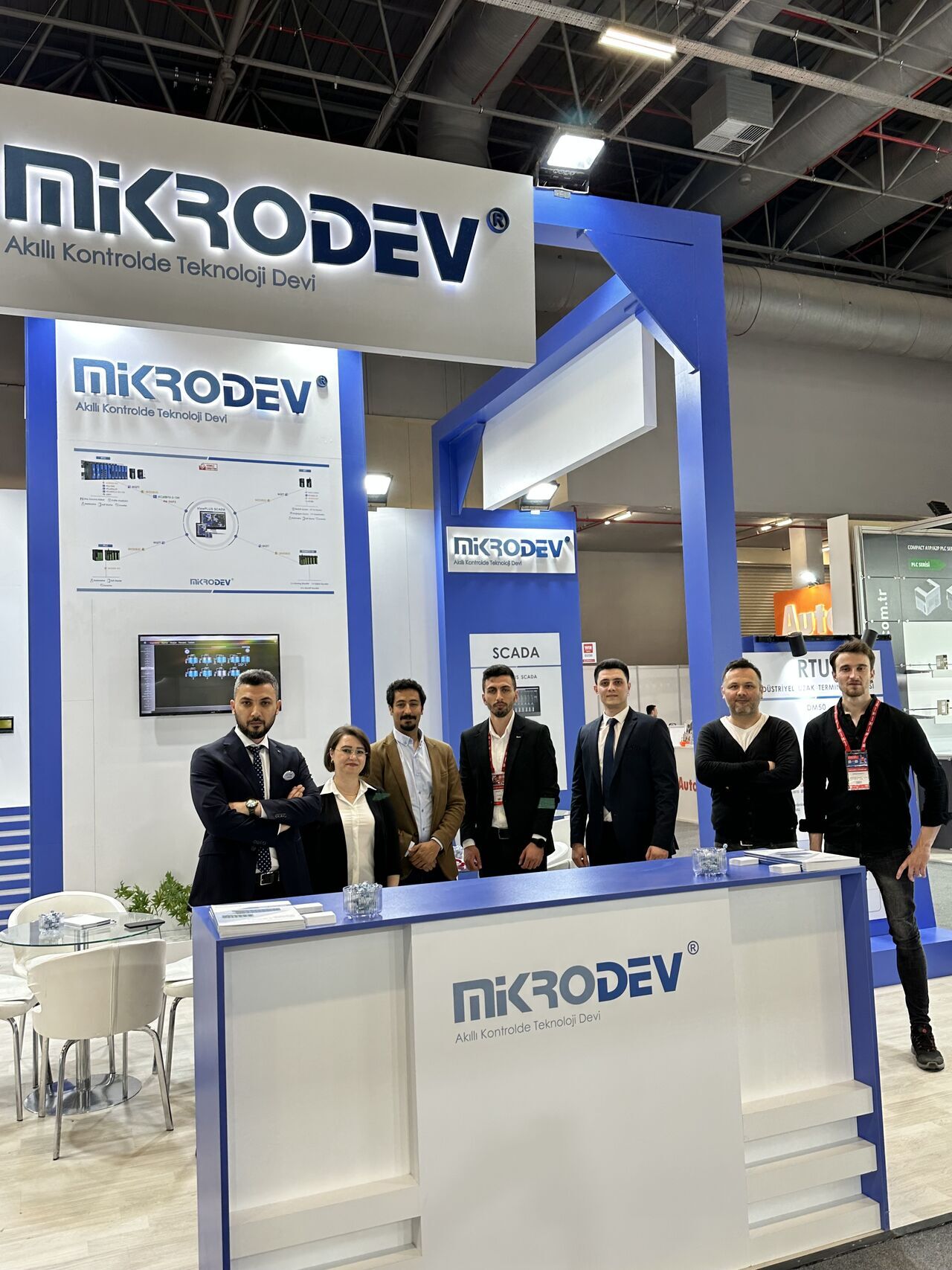
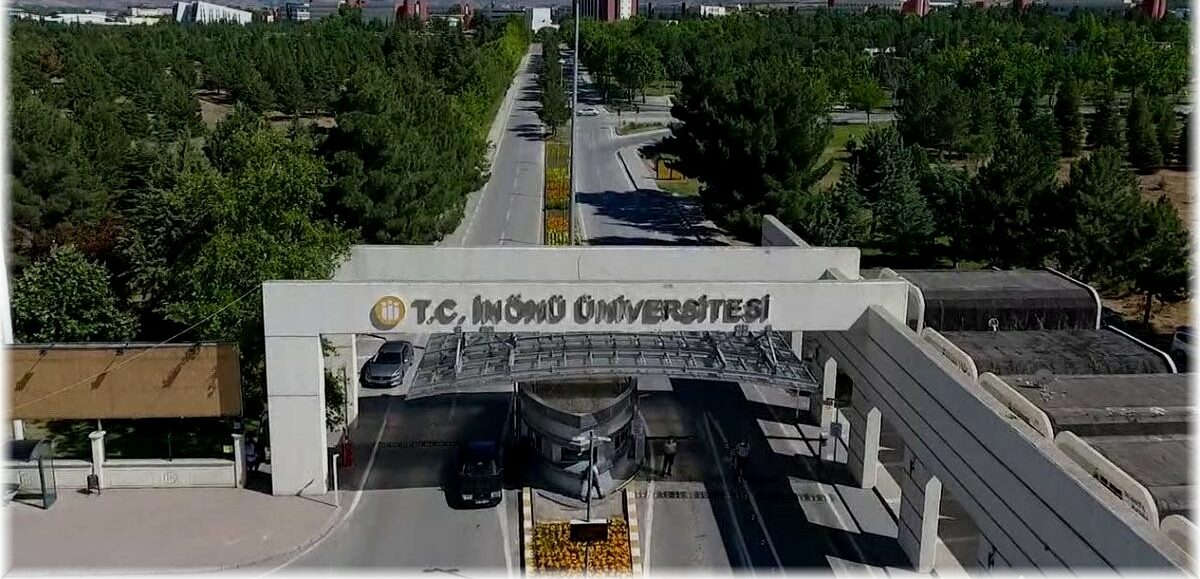
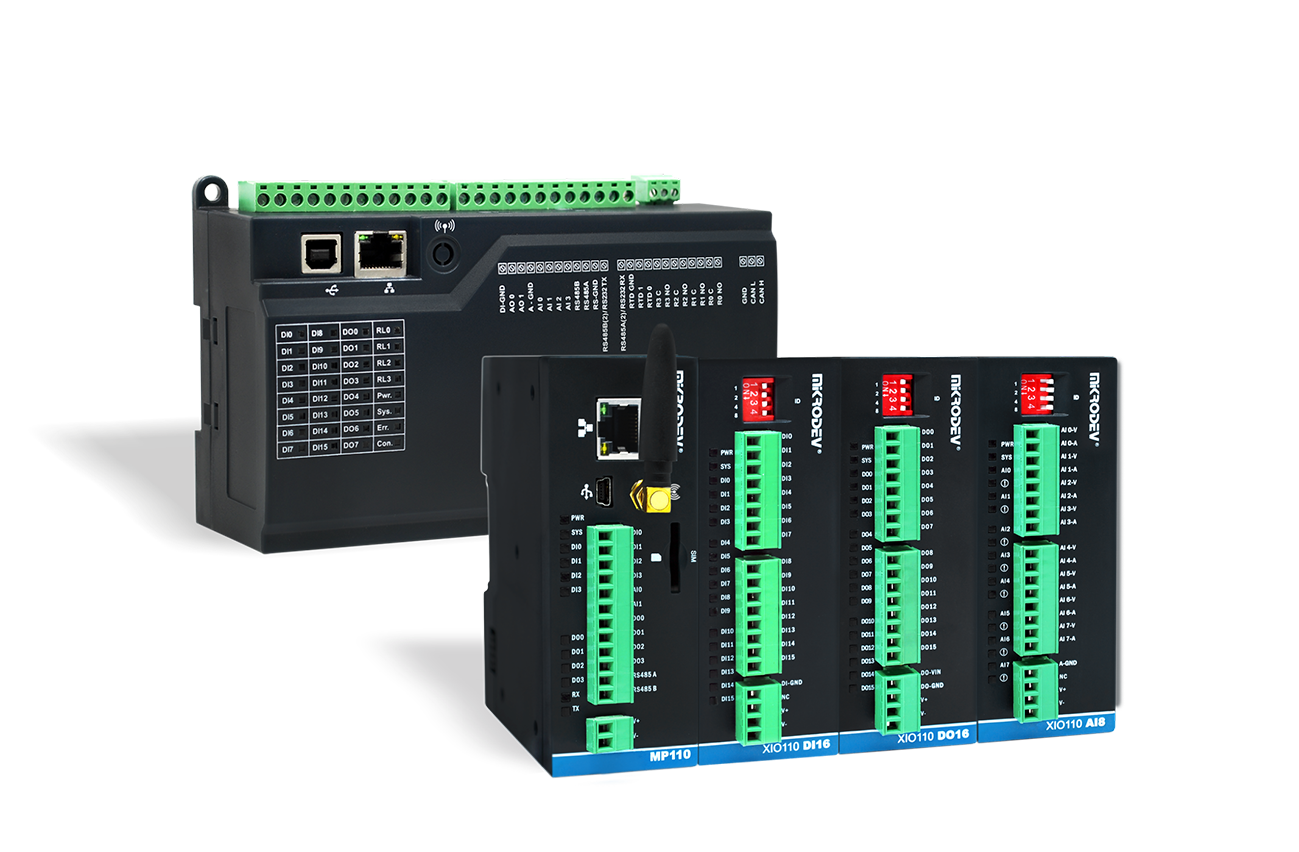
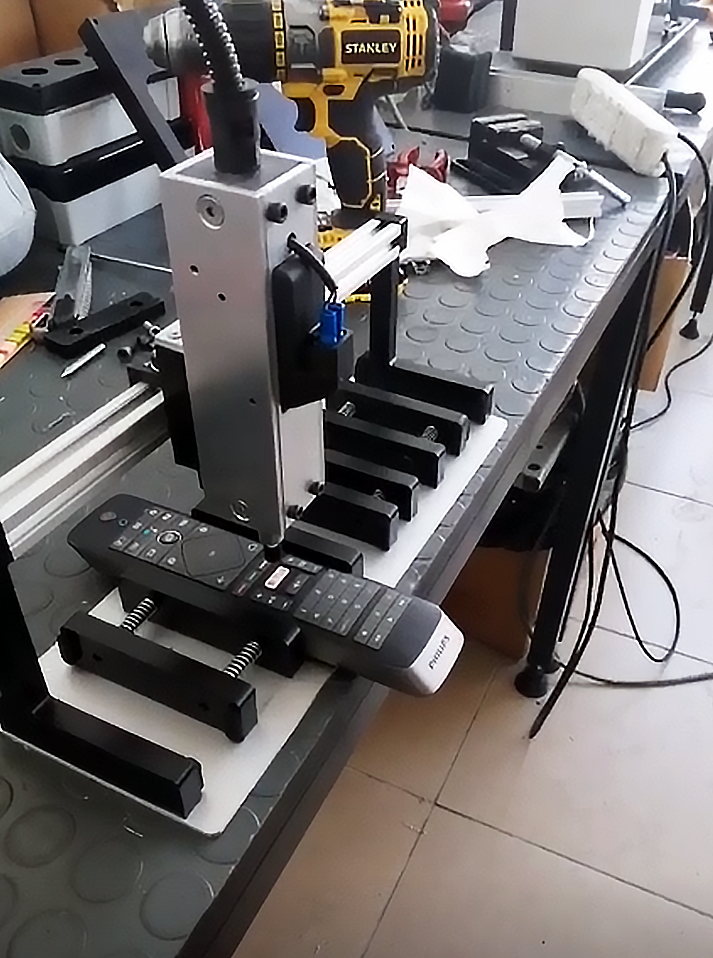
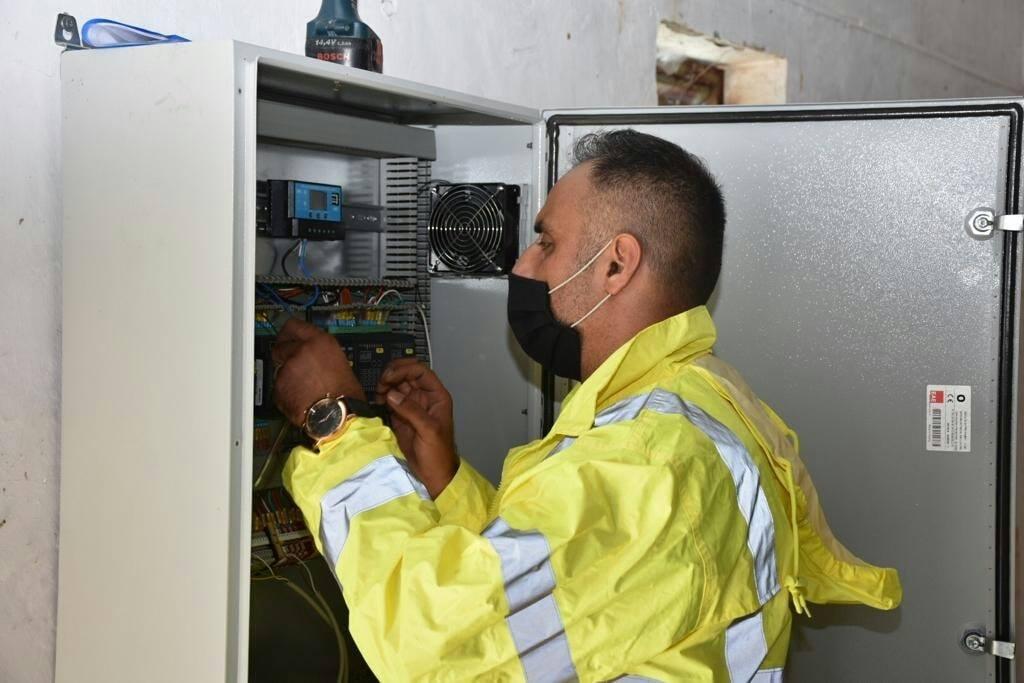
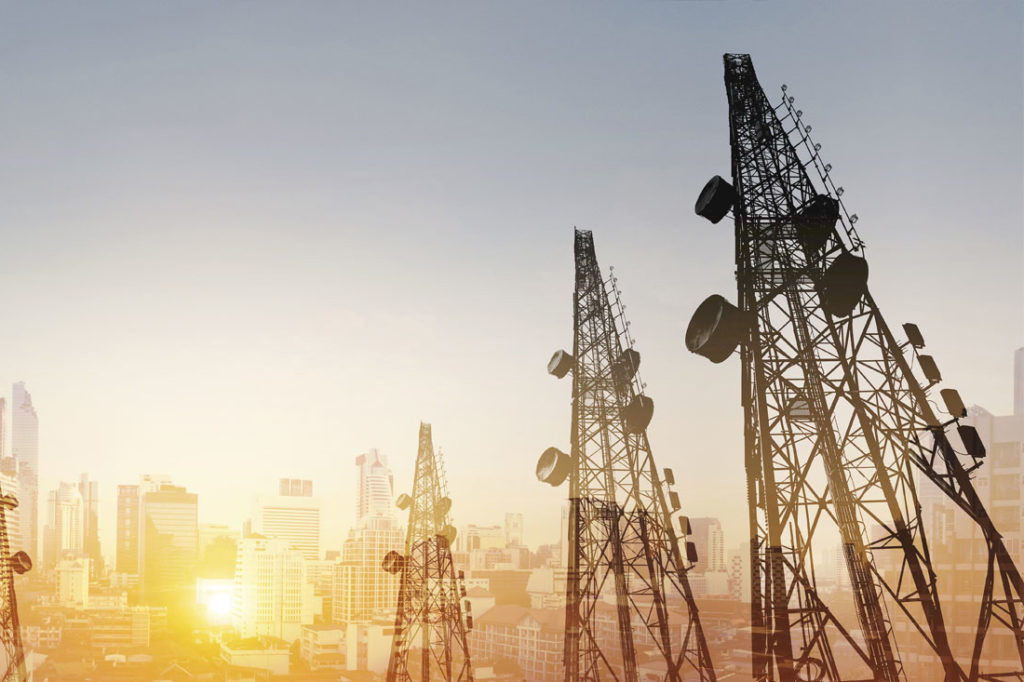
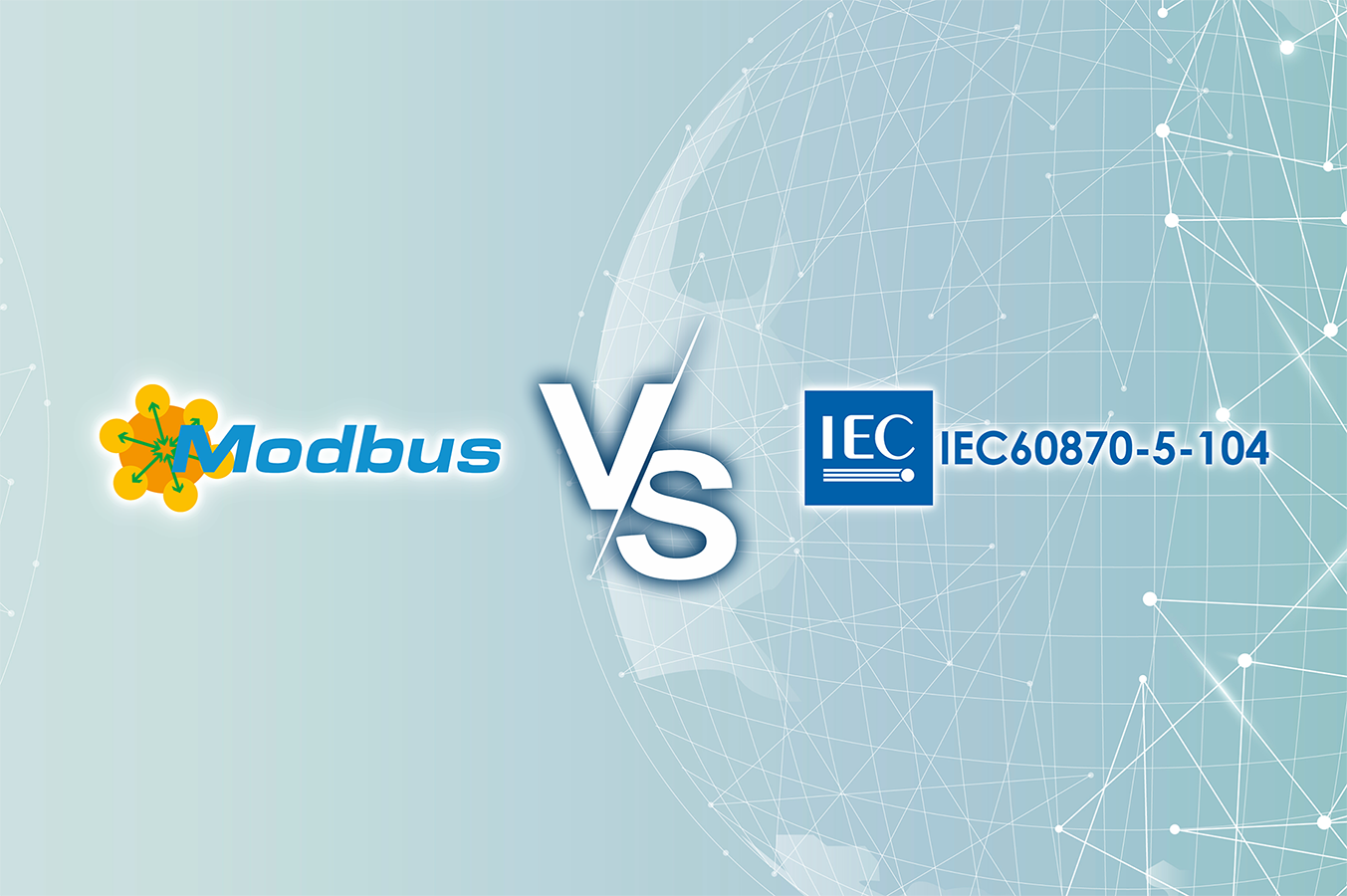
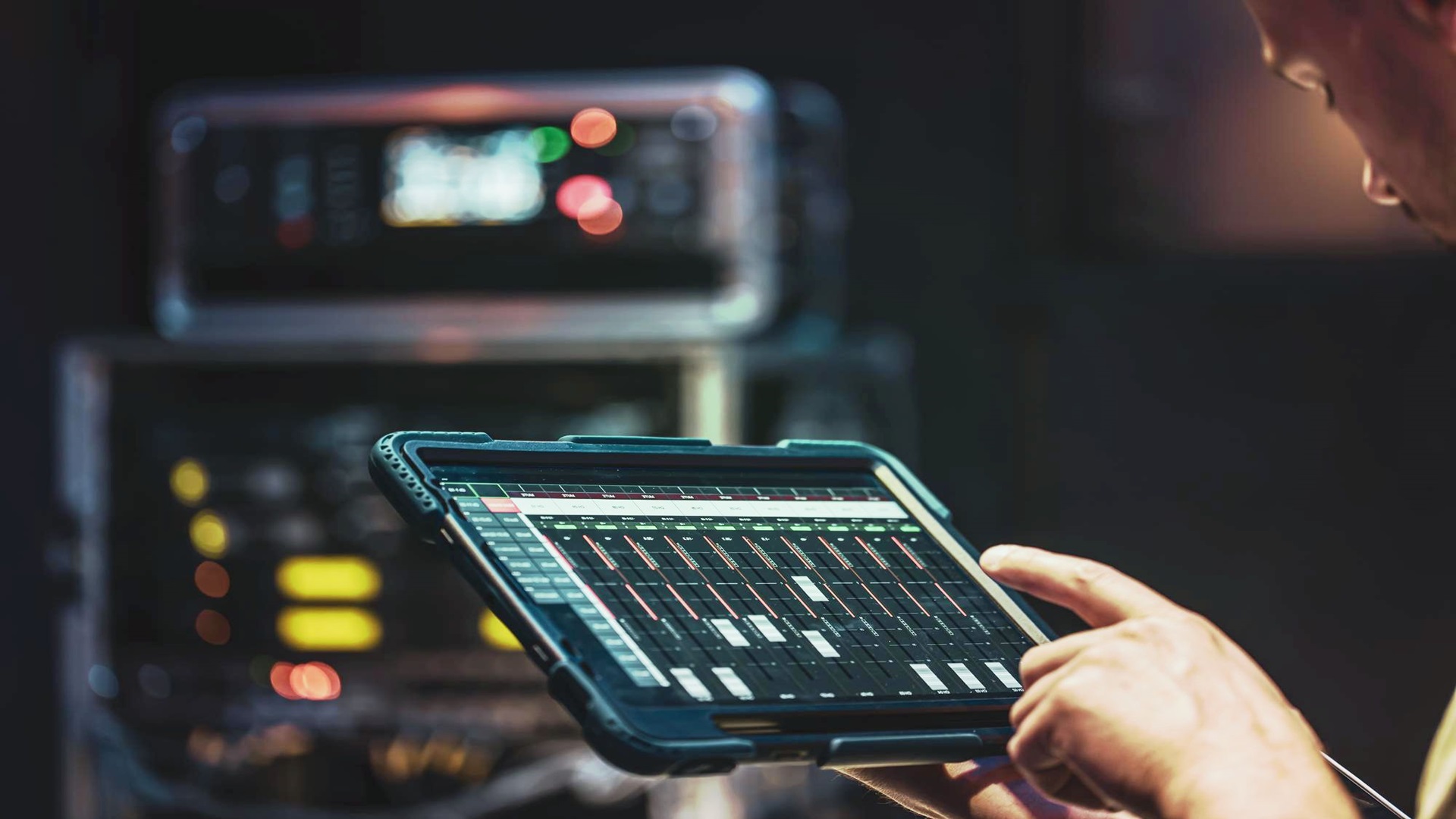
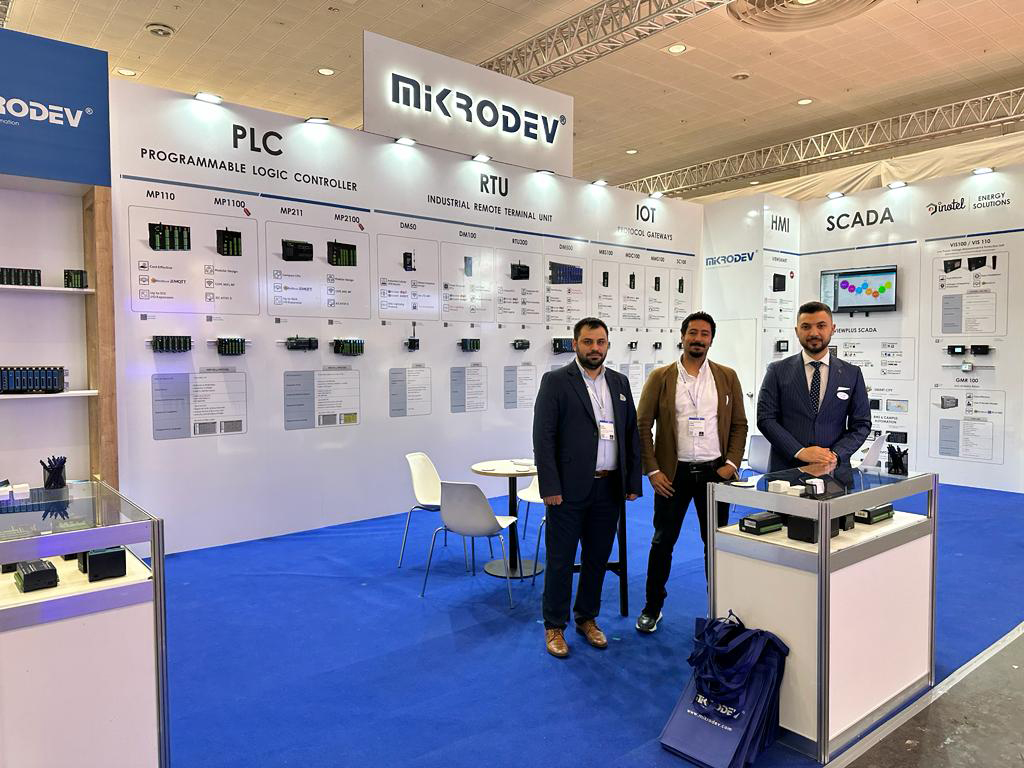